Thailand is making important strides in sustainable development with the event of its second 3D-printed prefabricated modular constructing. The work of SCG Cement Co.,Ltd is centered round the usage of low carbon mortar formulation. These superior concrete supplies have been particularly engineered to cut back the carbon footprint of development, demonstrating a dedication to each environmental sustainability and innovation within the area of 3D printing.
The venture’s give attention to integrating low carbon mortar with 3D printing know-how showcases how the development trade can transfer in direction of extra sustainable practices. By combining SCG Cement’s low-emission concrete formulation with cutting-edge 3D printing, this initiative is setting a brand new customary for eco-friendly constructing options in Southeast Asia.
Low Carbon Mortar: A Sustainable Basis for 3D-Printed Constructions
One of many standout options of this venture is the usage of low carbon mortar, a specialised concrete system developed by SCG Cement that considerably reduces the carbon emissions related to conventional concrete manufacturing. Because the main provider of concrete in Southeast Asia, SCG has developed this system by incorporating various supplies and waste merchandise that seize and retailer carbon dioxide, turning what was as soon as waste right into a helpful useful resource.
On this venture, low carbon mortar was utilized within the 3D-printed parts of the constructing, particularly within the manufacturing of light-weight mortar partitions. The concrete’s carbon footprint was considerably decreased whereas sustaining the structural integrity and sturdiness required for long-lasting buildings. The combination of low carbon mortar into 3D printing highlights the probabilities for decreasing emissions in large-scale development tasks with out compromising on high quality or effectivity.
By decreasing the necessity for conventional cement, which is a significant contributor to carbon emissions, this venture represents a step ahead in creating low-carbon constructing supplies. The 3D printing course of additionally ensures materials precision, that means solely the mandatory quantity of low carbon mortar is used, minimizing waste and additional contributing to the venture’s sustainability objectives.
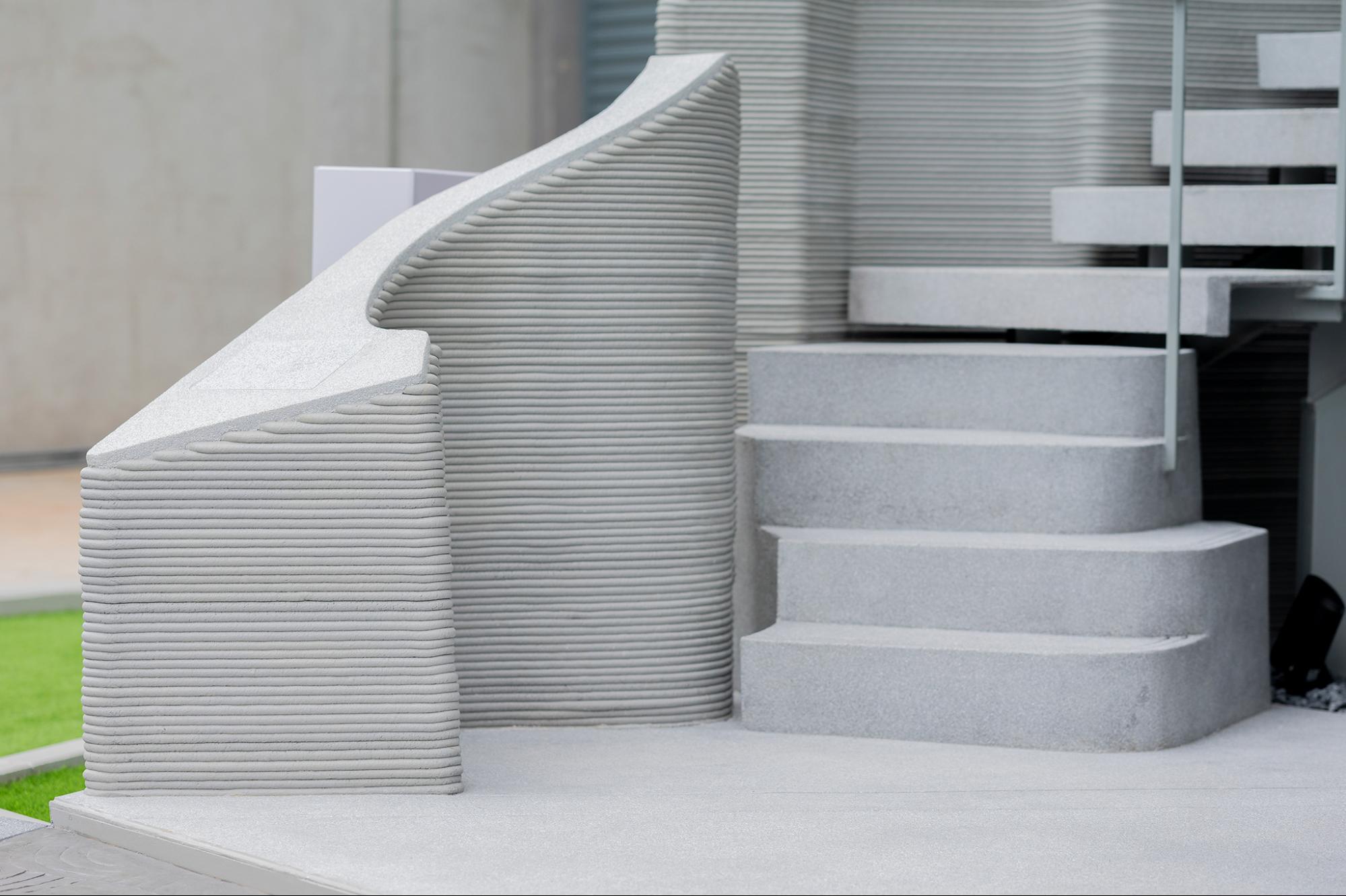
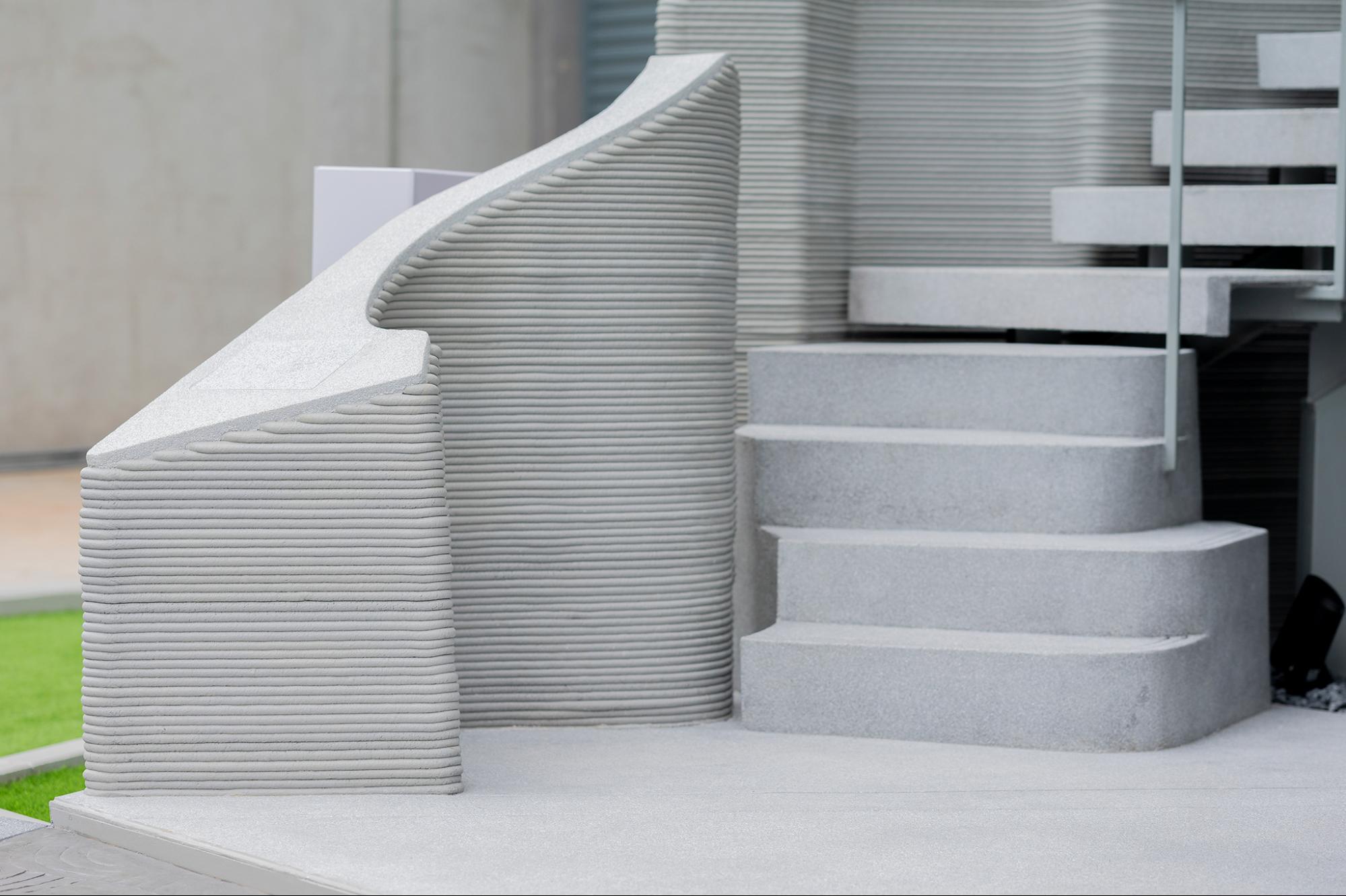
3D Printing and Low Carbon Supplies: A Highly effective Mixture for Sustainable Building
The mixture of low carbon mortar and 3D printing know-how brings quite a few benefits to the development course of. Utilizing prefabricated 3D-printed modules, the constructing’s structural parts have been produced off-site and assembled on location, drastically decreasing on-site labor and development time. This strategy not solely improves effectivity but additionally minimizes the environmental impression by limiting transportation and on-site waste technology.
Using low carbon mortar together with 3D printing marks a major development in sustainable constructing practices, providing a glimpse into the way forward for development. By specializing in decreasing the carbon footprint of supplies whereas profiting from the effectivity and precision of additive manufacturing, this venture serves as a mannequin for a way the development trade can transfer in direction of greener, extra eco-conscious options.
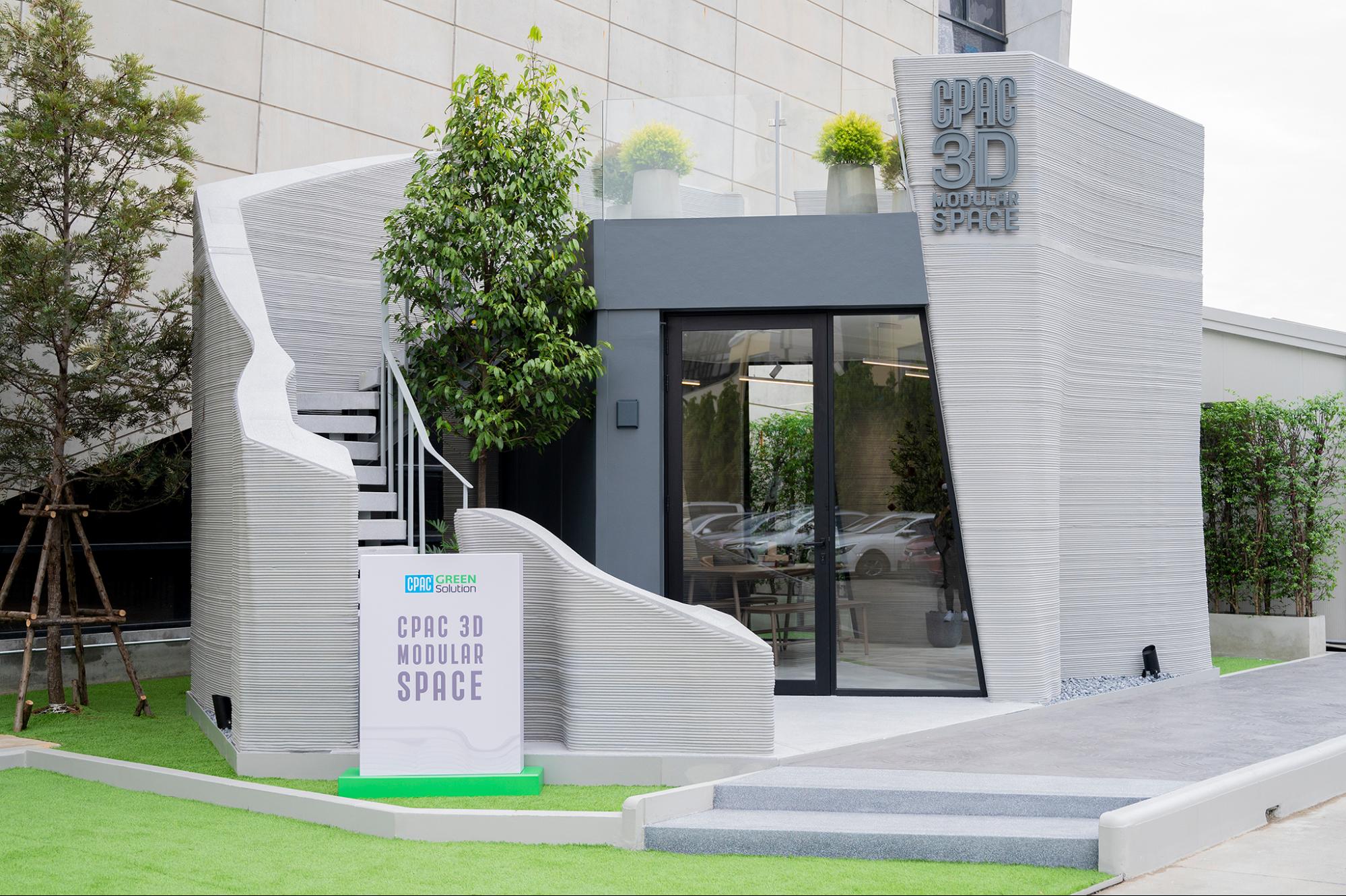
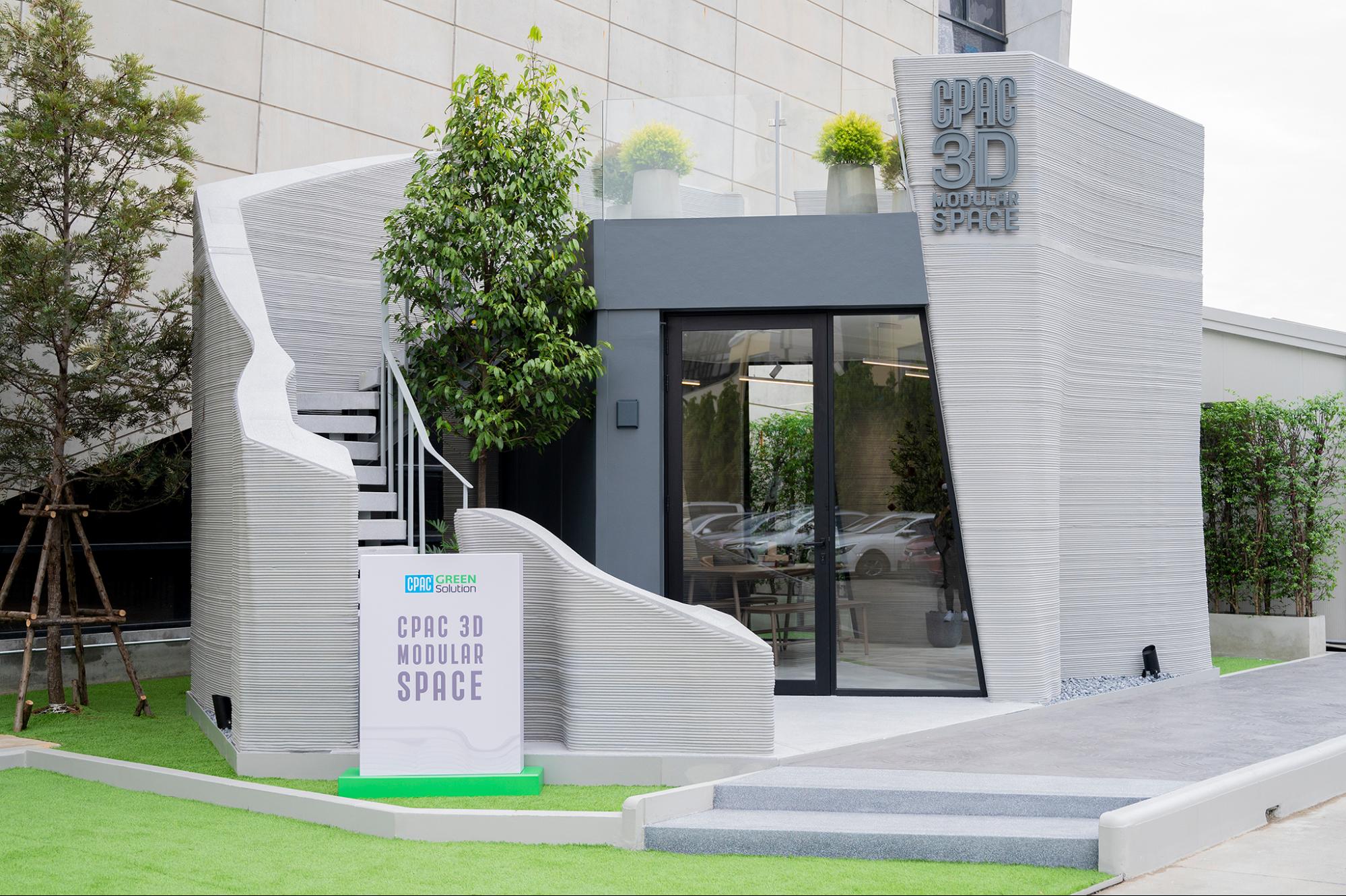
Design of a 3D-Printed Prefabricated Volumetric Constructing
The progressive constructing demonstrates the design freedom supplied by 3D printing, enabling distinctive architectural traits that conventional development strategies can not simply obtain. Its distinctive form, that includes a curved wall, highlights the mold-less design capabilities of 3D printing. With a usable space of 58 sq. meters, the construction includes six prefabricated modules, every tailor-made to particular sizes and features.


Designed for a public set up web site, the burden of every module was restricted to a most of 10 tons, guaranteeing ease of transportation and meeting. This modular strategy emphasizes practicality whereas showcasing the flexibleness of 3D-printed development know-how.
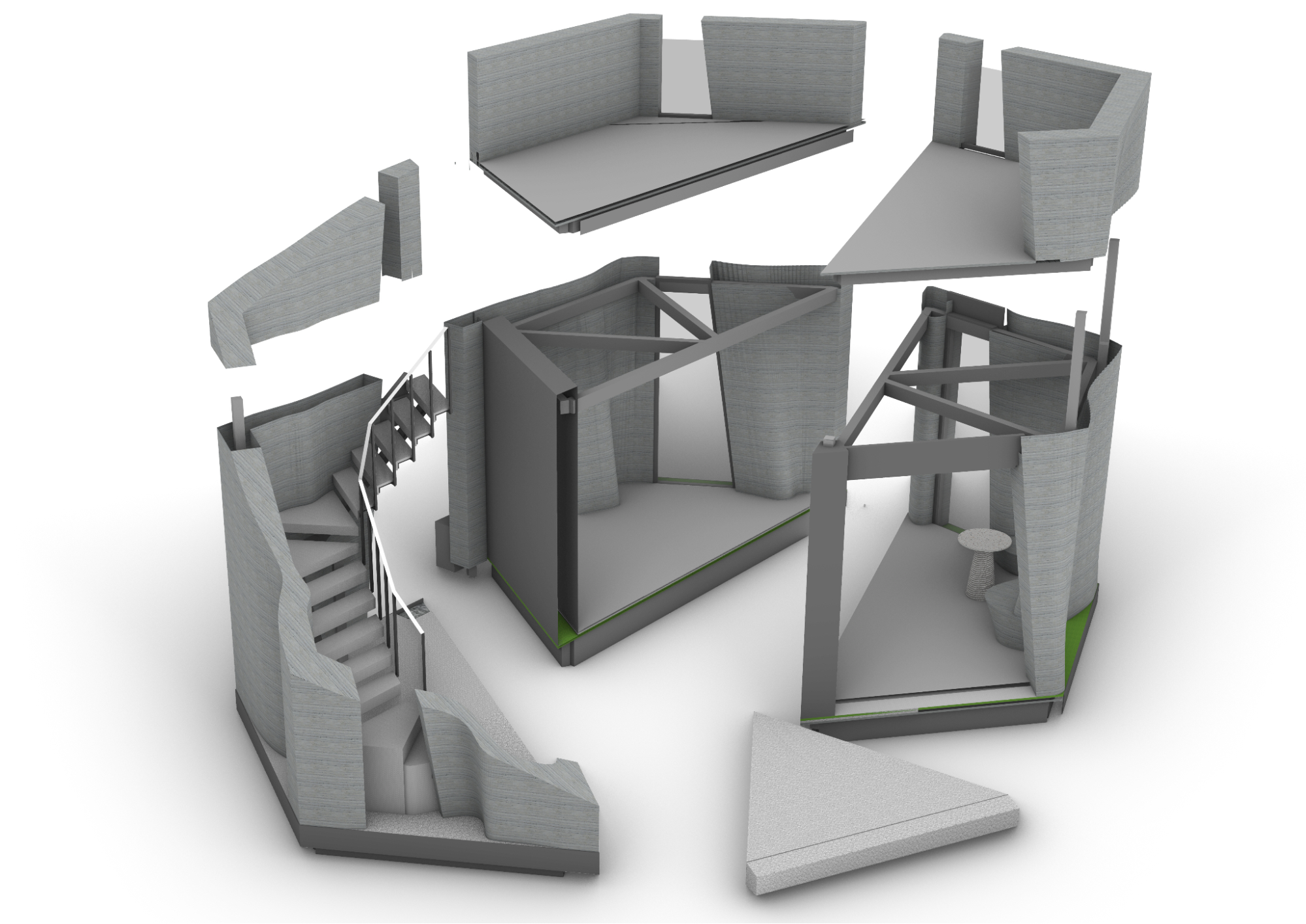
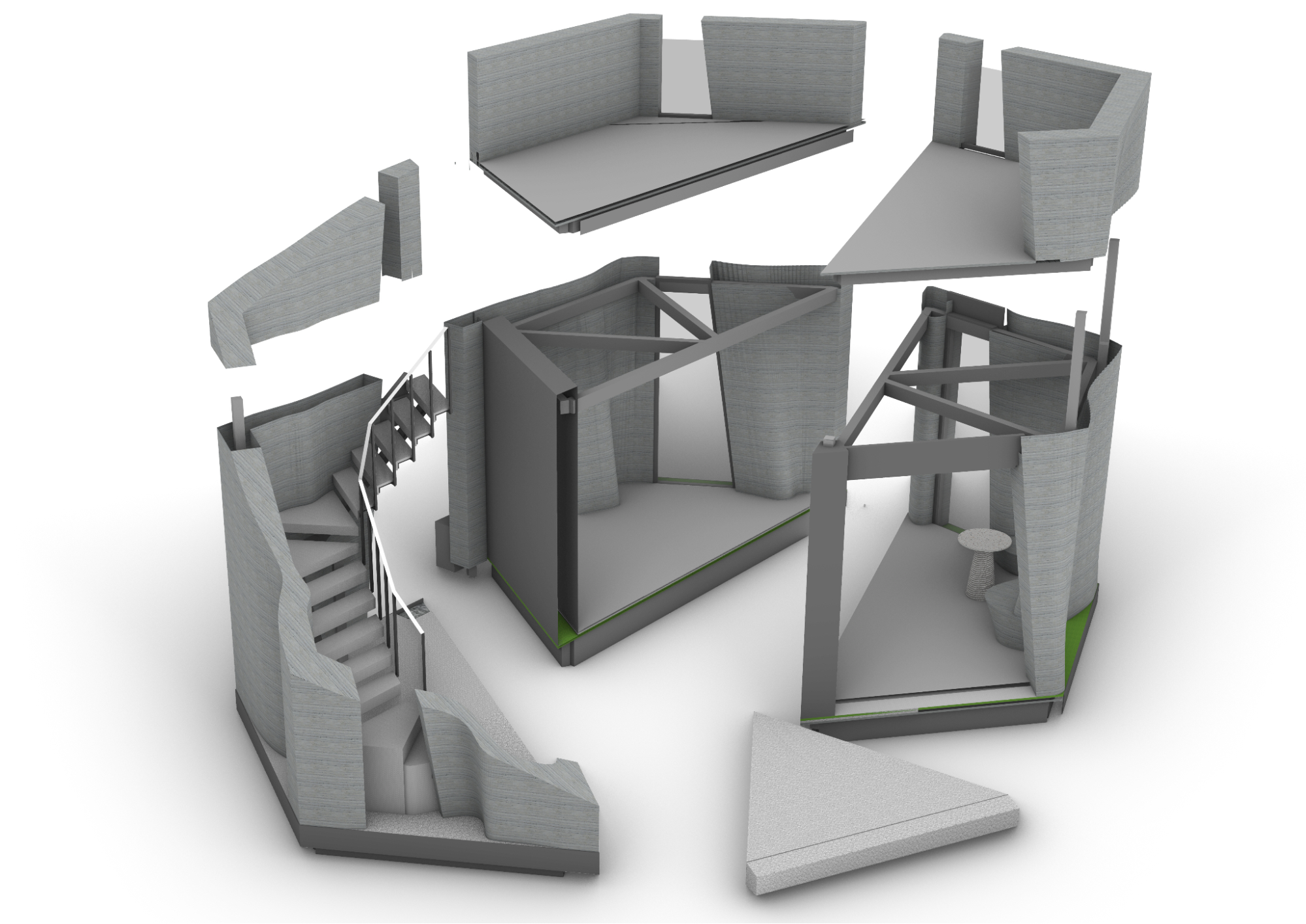
Idea and Structural Design
Supposed for residential use, the constructing is designed to assist a dwell load of 150 kg/m². Every module integrates a metal body construction, with sections joined by welding for stability. The dry joint system used to attach the modules varieties a moment-resisting body when assembled, guaranteeing sturdiness and efficiency.
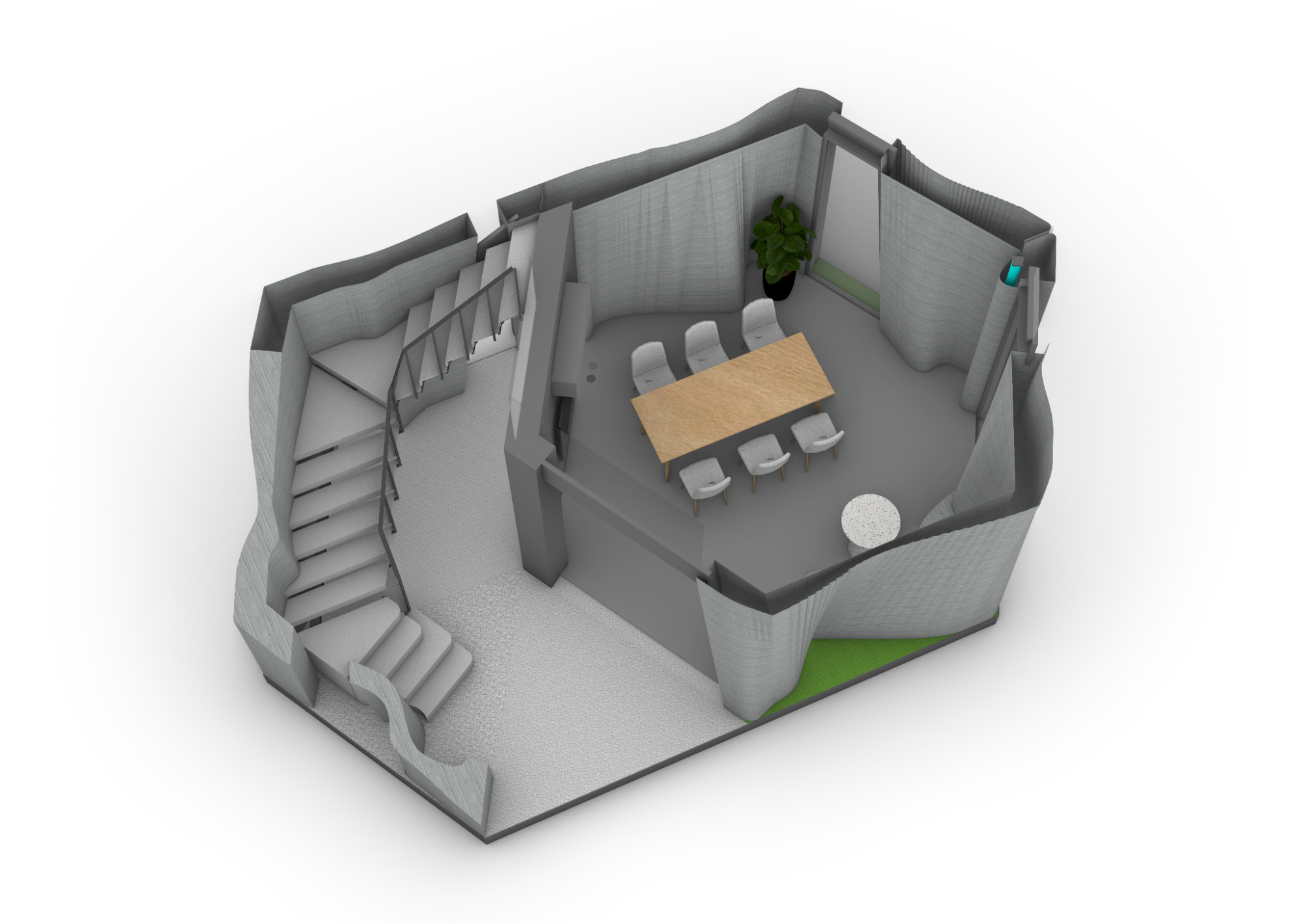
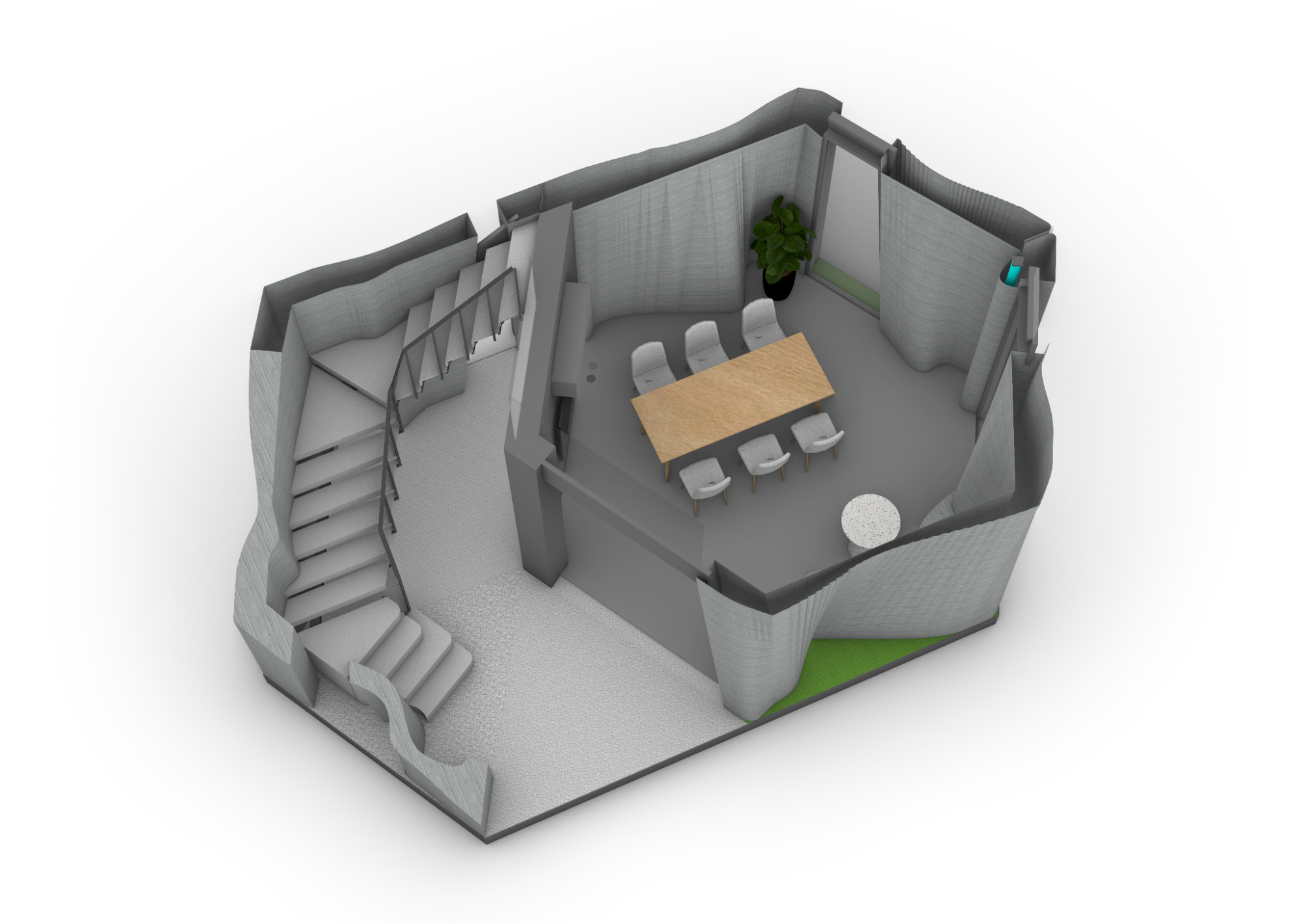
To make sure the security and integrity of the construction, complete analyses have been carried out. The metal framework was assessed utilizing Autodesk Robotic software program, whereas finite aspect evaluation (FEA) was performed on the 3D-printed partitions. These evaluations included findings from earlier analysis to look at the structural habits throughout lifting, transportation, development, and utilization phases.
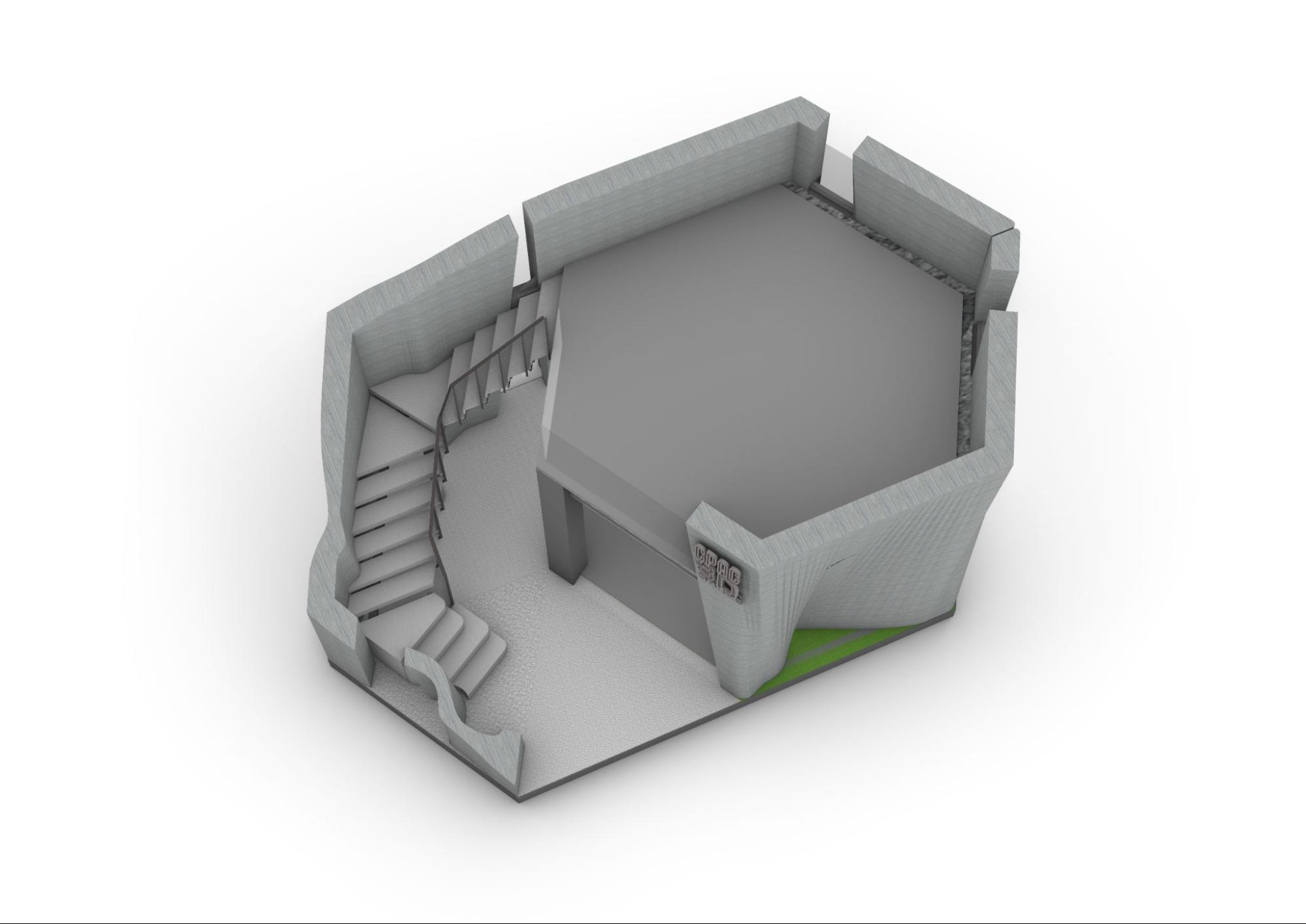
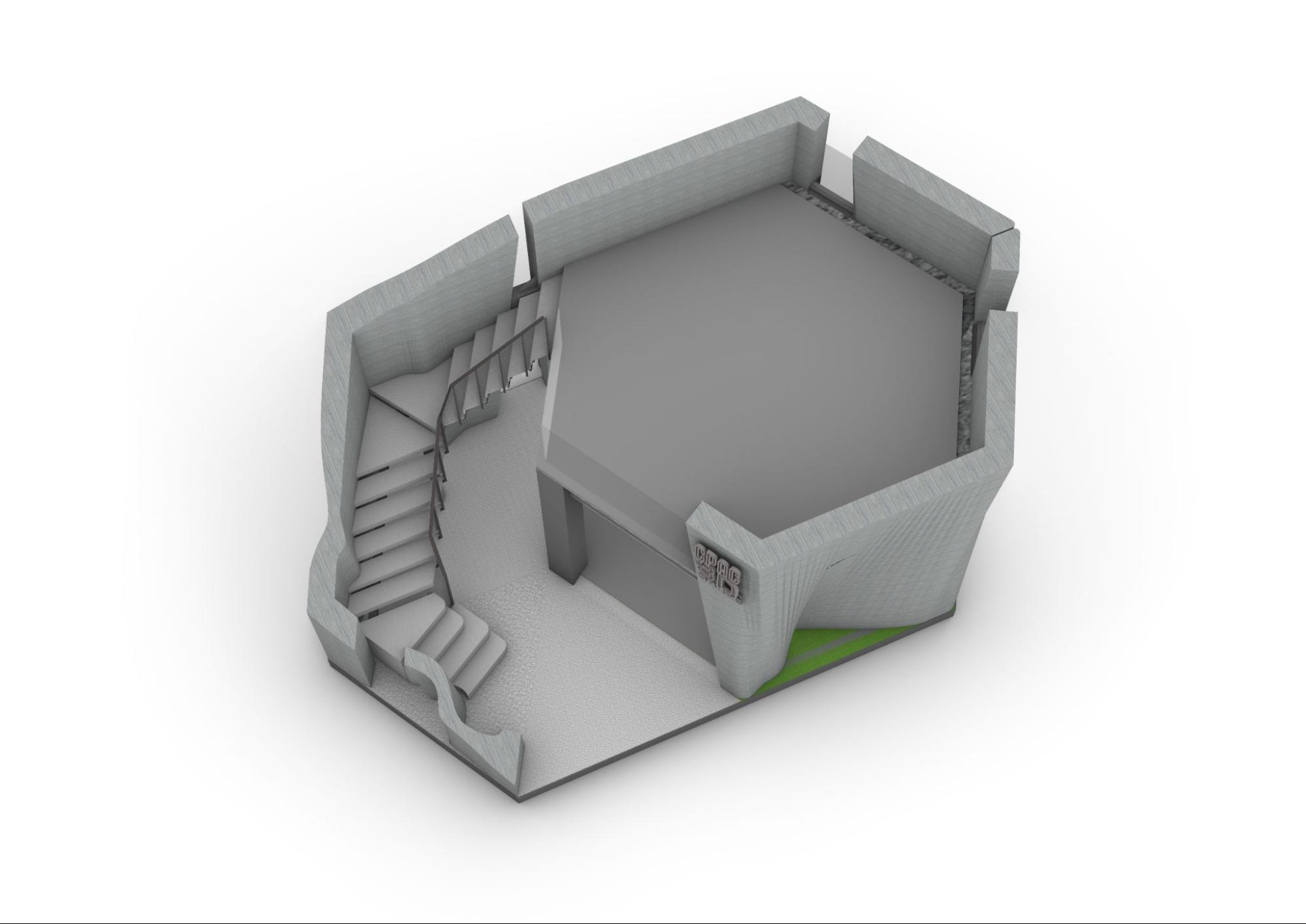
The joint particulars used on this constructing observe the design rules of PP3DVC development, prioritizing energy, leakage prevention, ease of meeting, and aesthetics. Collectively, these options spotlight the synergy between 3D printing and conventional structural parts, setting a benchmark for contemporary prefabricated constructing design.
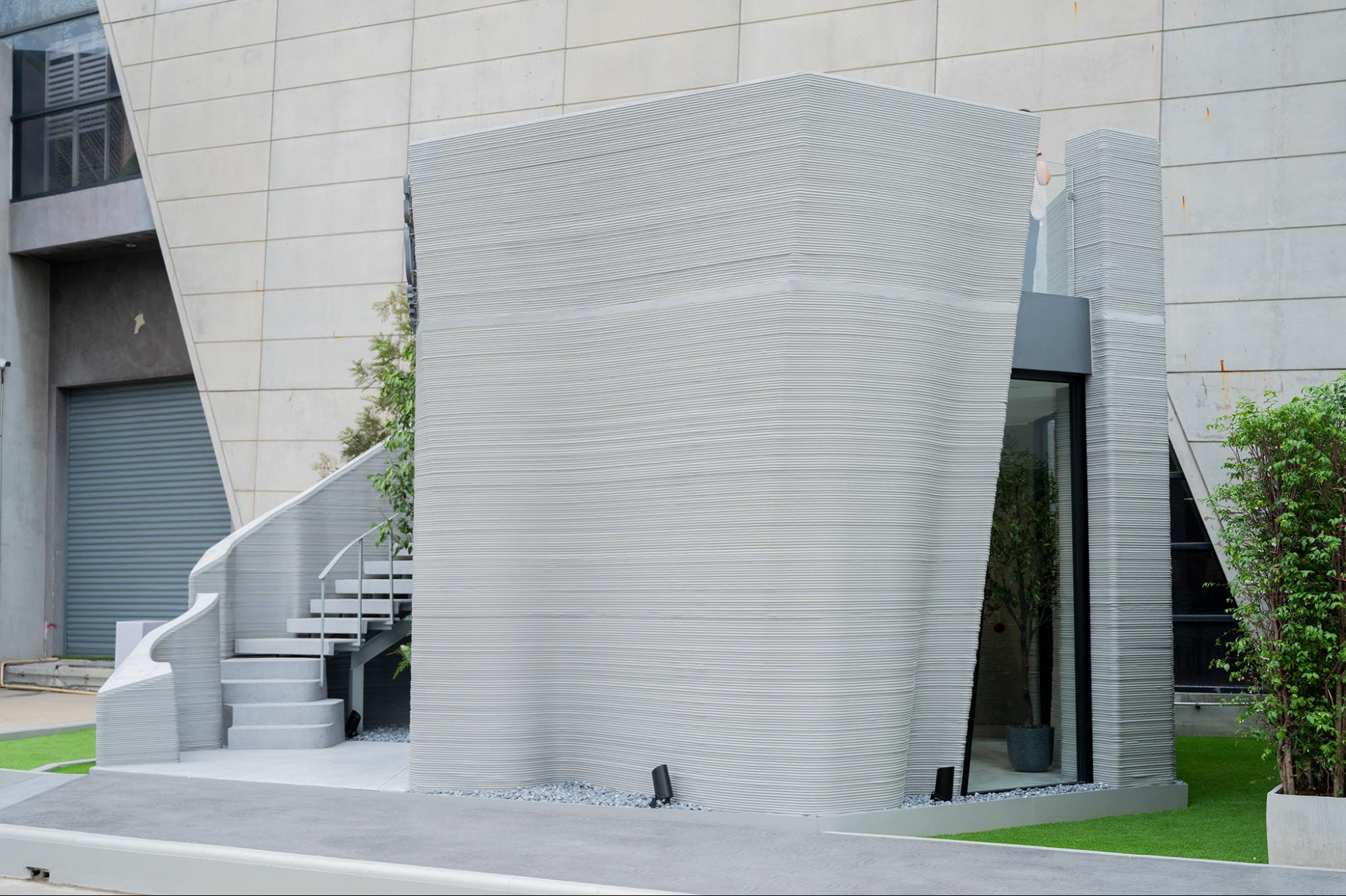
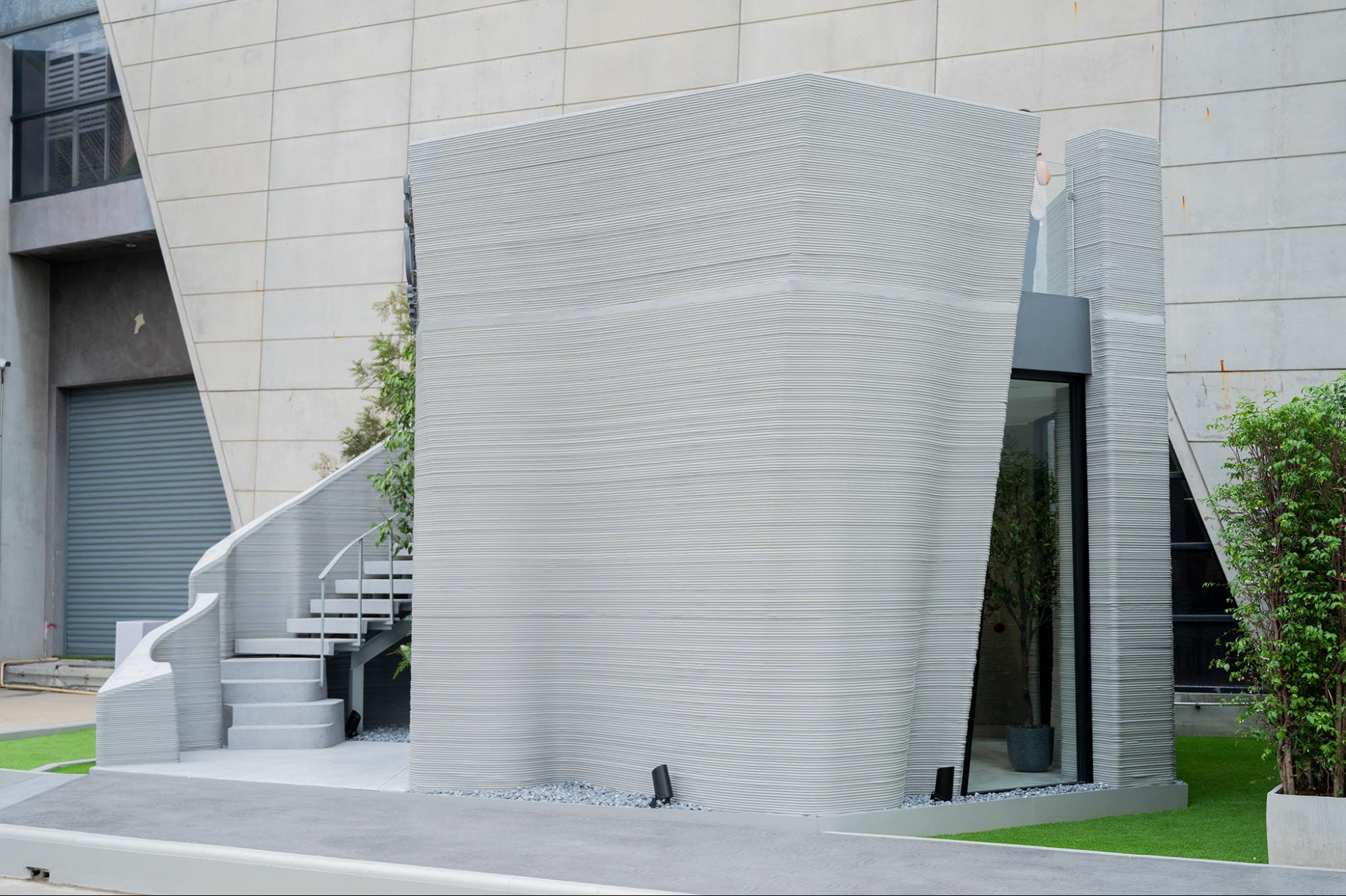
Environment friendly On-Web site Building Course of
The development course of was divided into three principal phases: web site preparation, manufacturing unit fabrication, and on-site set up. Web site preparation, accomplished in 10 days, occurred concurrently with module manufacturing, which reached 95% completion throughout this time. Fabrication of the six modules—together with flooring, 3D-printed partitions, metal constructions, and off-site ending—was accomplished in 33 days. As soon as fabricated, the modules have been transported 150 kilometers to the positioning, the place set up took solely 5.5 hours. Last on-site ending was accomplished in 7 days, leading to a complete development time of 41 days, with 65% of the work accomplished off-site.
When in comparison with conventional development strategies, the 3D-printed PPVC strategy considerably decreased constructing time, reducing the schedule by 48% in comparison with brick-and-mortar development and 54% in comparison with precast concrete, saving between 25 and 38 days.
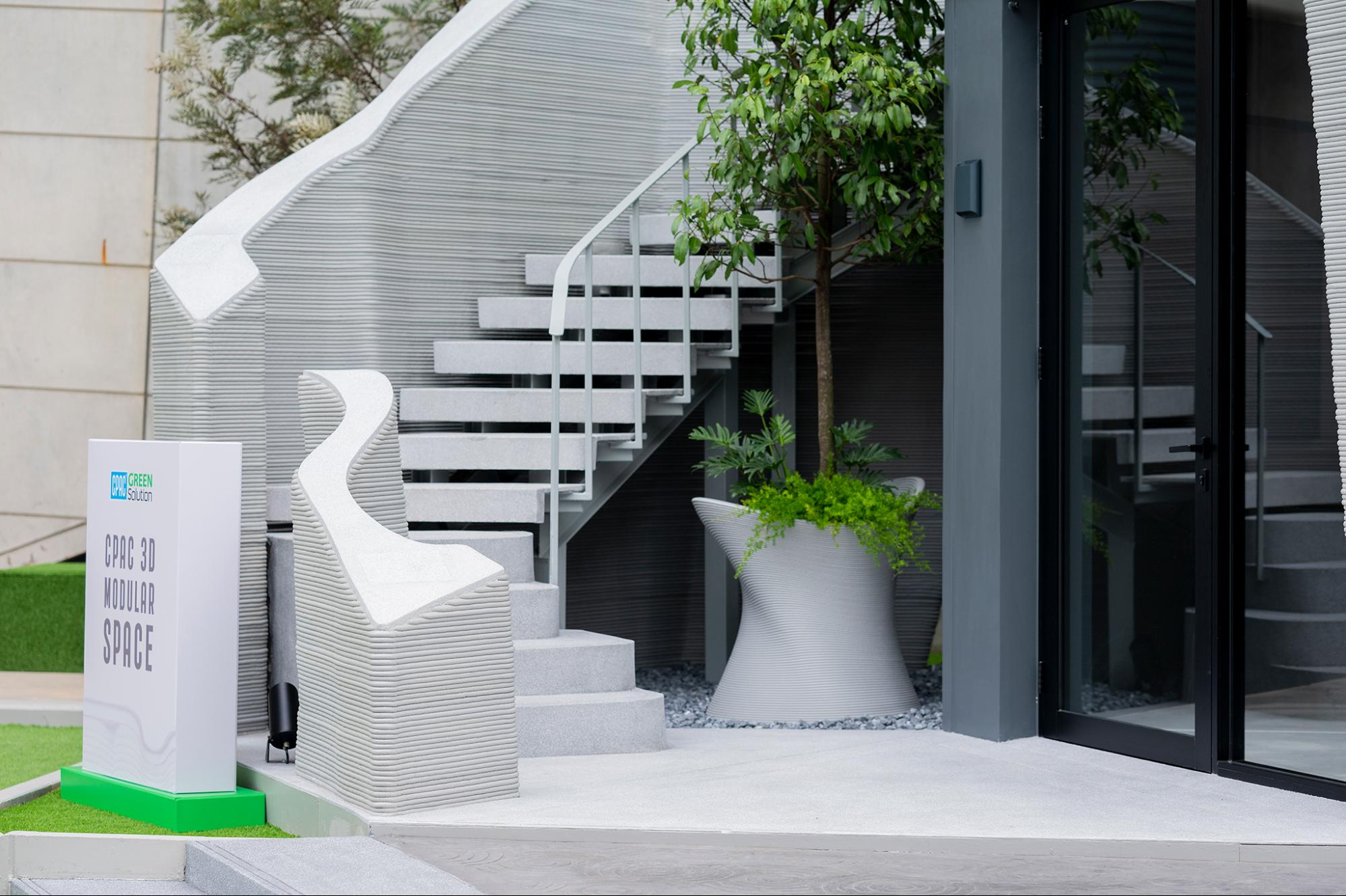
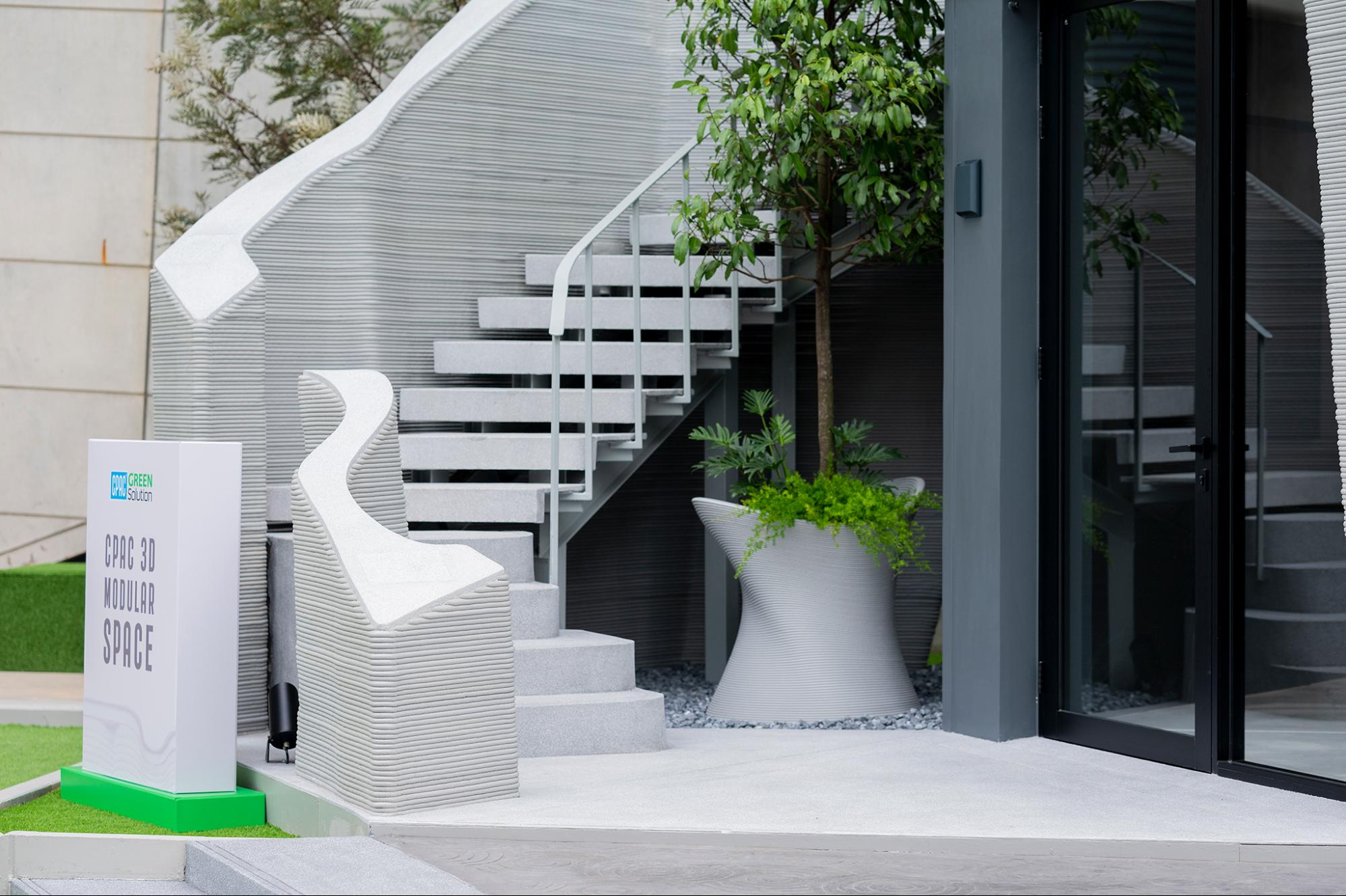
SCG Cement Co.,Ltd Encourages Trade Adoption of 3D Printing for a Sustainable Future
Thailand’s 3D-printed modular constructing venture highlights the highly effective position that low carbon supplies and 3D printing can play in shaping the way forward for development. SCG Cement Co.,Ltd because the driving pressure behind this initiative, encourages trade leaders, builders, and designers to contemplate the advantages of adopting comparable strategies of their tasks. With local weather change driving an pressing want for sustainable options, SCG Cement Co.,Ltd believes that combining 3D printing know-how with low carbon supplies provides a compelling path towards reaching international carbon discount targets.
SCG Cement Co.,Ltd invitations stakeholders to discover how these progressive approaches can contribute to sustainability efforts whereas additionally enhancing effectivity, decreasing materials waste, and producing resilient constructions. By embracing low carbon mortar and 3D printing, the development trade could make a major impression on decreasing emissions and minimizing environmental impression with out compromising high quality.
By committing to progressive, low-emission constructing options like these demonstrated on this venture, we are able to collectively work in direction of a greener, extra sustainable future for the following technology.
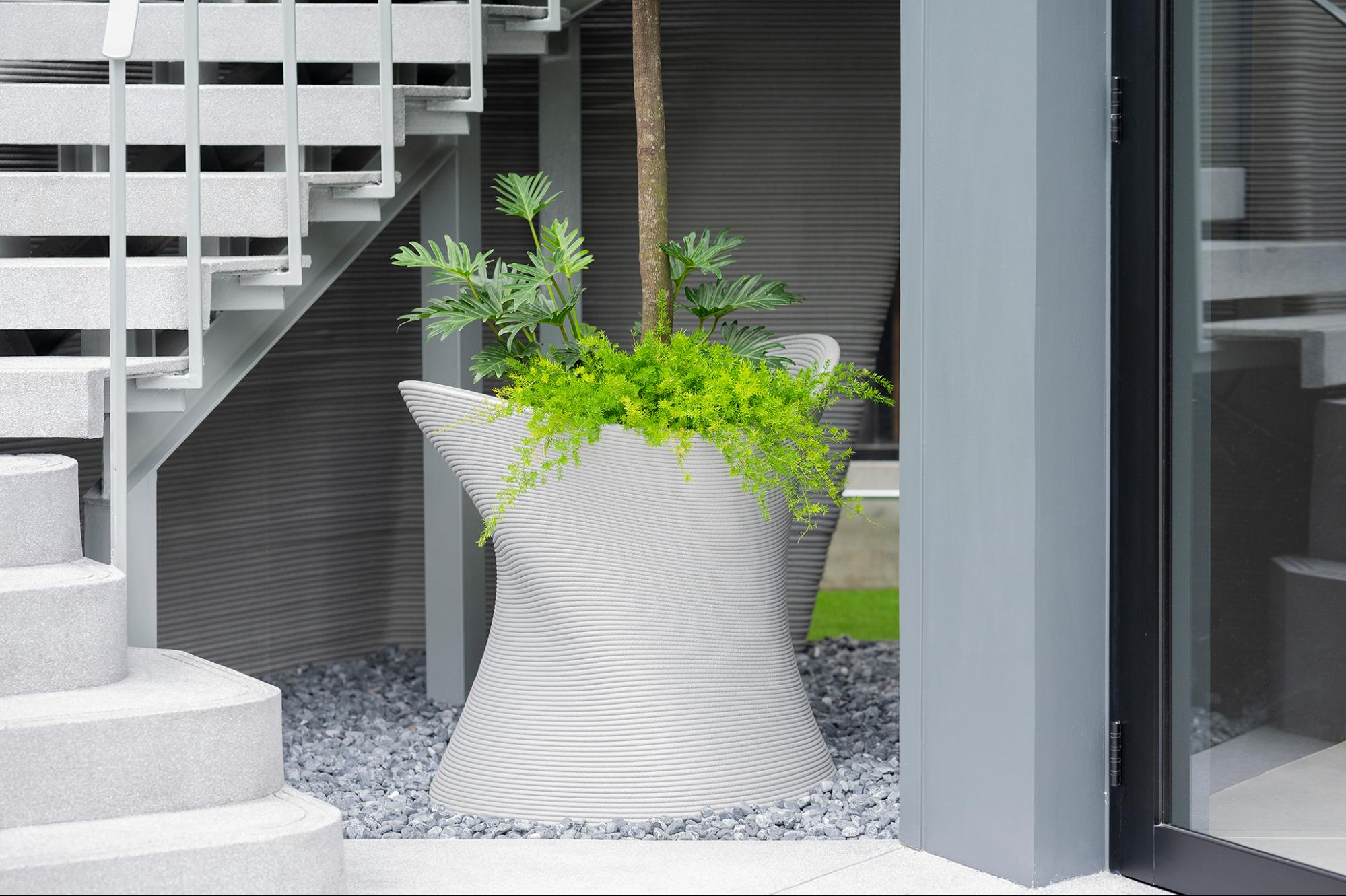
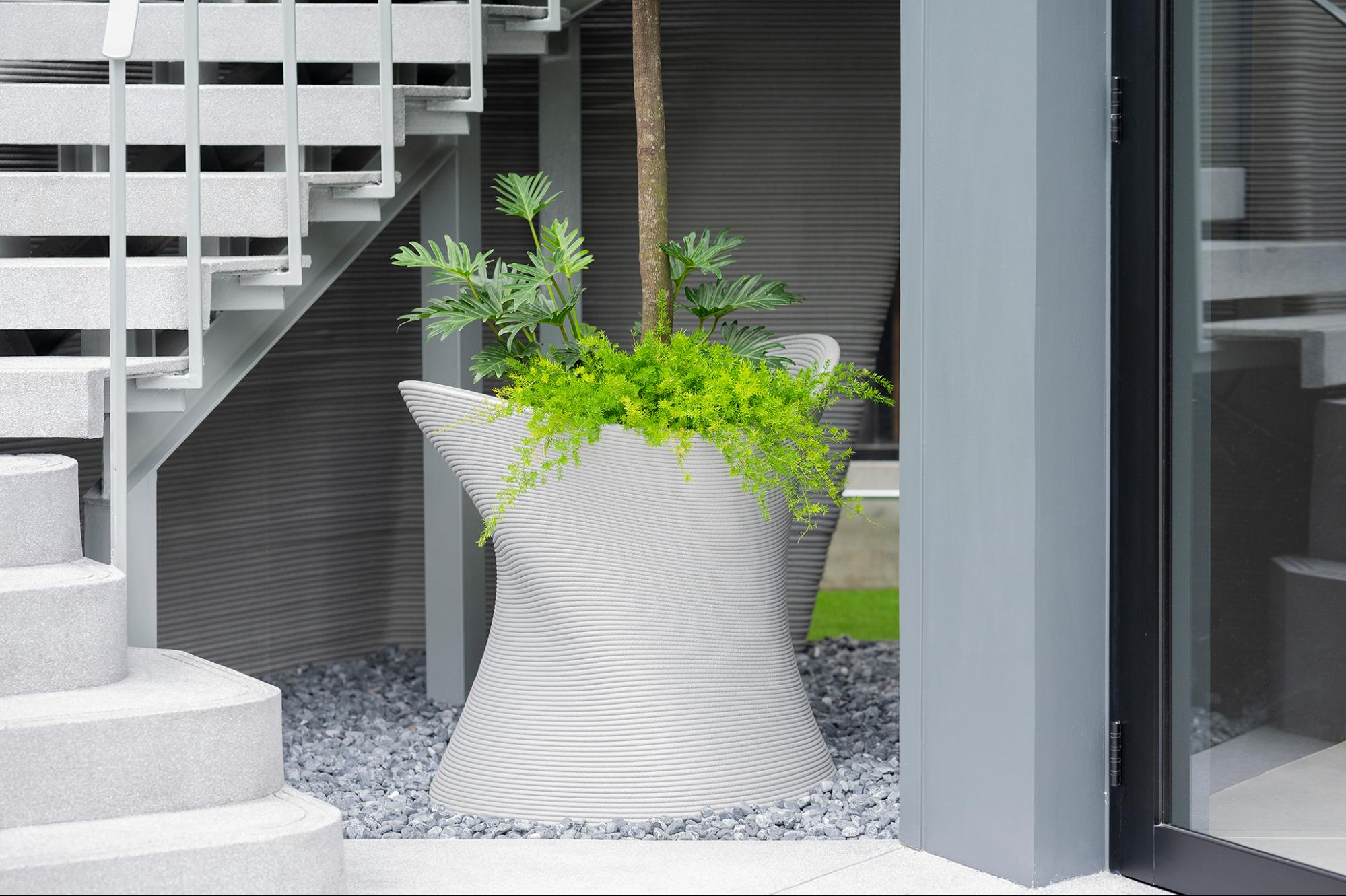
Entry the Full Use Case
For these considering a deeper dive into the technical facets of this venture, the whole use case is obtainable upon request. You may contact (pattarut@scg.com). This doc provides additional insights into the challenges encountered throughout the design and manufacturing phases and offers an in depth take a look at the mixing of biochar into the development supplies. It additionally covers logistical concerns, together with module transportation and on-site meeting, which performed a important position within the success of this progressive initiative.
References
This venture builds upon prior analysis and methodologies outlined in key tutorial works. Notable references embrace:
Jongvisuttisun, P., Chaiyapoom, P., Jiramarootapong, P., Meemuk, Okay., Snguanyat, C. (2024). The Second 3D-Printed Prefabricated Prefinished Volumetric Building Constructing in Thailand: A New Sustainable and Environment friendly Strategy for a Low-Rise Prefab Modular Constructing. In: Lowke, D., Freund, N., Böhler, D., Herding, F. (eds) Fourth RILEM Worldwide Convention on Concrete and Digital Fabrication. DC 2024. RILEM Bookseries, vol 53. Springer, Cham. https://doi.org/10.1007/978-3-031-70031-6_4