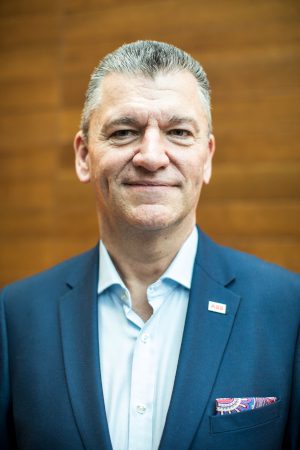
Efforts to make sure the continuity of at the moment’s mission-critical industrial operations are blunted by the burden of getting old and more and more complicated electrical programs. ABB’s Lee Todd explains how forward-looking approaches to tools upkeep can reward organizations with optimized enterprise continuity and better sustainability in addition to lowered prices.
Unplanned lack of manufacturing is a contingency that’s seldom welcomed by organizations, their prospects and shareholders. Halting a chemical, pharmaceutical or different industrial course of on account of sudden electrical failure means an instantaneous loss in revenues. And other than the short-term business penalties, companies like knowledge facilities – the place five-nines uptime is an crucial slightly than a nice-to-have – face the prospect of deeper and longer-term influence to their company repute.
Even a extremely skilled upkeep engineer or plant operations supervisor might have little or no prior indication that important electrical parts are about to fail. Whereas the primary signal of an impending drawback is usually a tripped circuit breaker, that remoted occasion reveals subsequent to nothing concerning the underlying reason behind the difficulty. Reclosing the breaker might enable manufacturing to renew within the fast time period. Nevertheless it gained’t repair the underlying reason behind a critical underlying concern that’s about to get a complete lot dearer very quickly.
The character of recent enterprise highlights the intrinsic issues related to conventional electrical upkeep methods. Routine tools inspections are sometimes carried out at periodic intervals, sometimes accompanied by the prescriptive substitute of kit or particular person parts based on a specified timetable. This regime assumes a imply time between failure for parts that’s constant and predictable. And this can be a presumption that’s far faraway from the realities of plant operations the place failure can, and infrequently will, happen lengthy earlier than – or after – the producer’s specified estimate.
Time-based upkeep methods can not assure {that a} specific half gained’t fail earlier than its allotted time. Equally, they’re an costly and typically ineffective use of firm assets. Changing an getting old element that’s nonetheless in completely usable situation, no matter its acknowledged working life, achieves little. It’s expensive by way of assets and human capital, tying up operations and upkeep employees on an unneeded swap-out whereas consigning a completely functioning half to landfill, months or years earlier than its allotted time. And whether or not it’s wanted or not, scheduled upkeep typically brings productiveness to a standstill for hours or days, biting into revenues and profitability that almost all companies can sick afford.
Reflecting the growing scale and class of recent plant operations, the bounds of time-based and reactive upkeep schedules are amplified additional as electrical programs turn into bigger and extra complicated. Trade’s progressive digitalization poses extra challenges, heightening the necessity for electrical programs to carry out with out interruption to keep away from the chance of dropping treasured insights collected from instrumentation and management programs about course of and plant efficiency.
The challenges of securing manufacturing continuity and resilience are additional exacerbated by the necessity for organizations to embed sustainability and circularity throughout all areas of their operations. Aggressive pressures and regulatory scrutiny imply that enterprise house owners face an crucial to enhance their power effectivity, cut back carbon emissions and reduce waste. Coupled with continued volatility in power costs, these components are encouraging extra industrial organizations to energy their important electrical programs utilizing renewable sources of power. This will both be achieved by buying inexperienced electrical energy straight from utility firms or, more and more, by companies producing their very own electrical energy on web site. Putting in era capability, typically within the type of wind generators or photo voltaic arrays, affords plant house owners better power safety in addition to the chance to avoid wasting on shopping for electrical energy from different sources.
However whereas this ‘self-serve’ power technique pays dividends for organizations’ sustainability – and their backside line – it introduces its personal extra challenges. Making certain the dependable operation and administration of a plant’s important electrical programs turns into an much more complicated endeavor when integration of renewable sources is added to the image. In a survey of business organizations carried out by ABB in 2023, a major proportion of respondents confirmed that they’re struggling to cope with the complexities of managing a number of sources of power together with renewables. Within the case of knowledge facilities, for instance, 40% of these surveyed cited defending the integrity of their energy provides as being amongst their most daunting challenges.
In widespread with many engineering-led trade sectors, an growing abilities scarcity is making it tougher to determine and retain suitably expert personnel. Tens of hundreds of veteran electrical programs specialists are retiring, taking with them many years of sensible expertise and deep data of extremely specialised electrical programs present in factories, energy vegetation and different industrial amenities. This pool of experience is leaving the trade sooner than it’s being changed, leaving employers throughout many industries struggling to fill a yawning expertise hole. With out this in-depth data of complicated electrical programs and their interactions with wider plant operations, a youthful era of newly-qualified can wrestle with the challenges of optimizing and sustaining legacy electrical programs which will have been initially specified and put in earlier than they have been born.
In-house engineering and upkeep employees also can wrestle with the speedy tempo of electrification expertise. Elements, working practices and rules are continually evolving, with the end result that specialist data about complicated programs can turn into shortly outdated. That is notably with the case with conventional reactive upkeep that’s closely reliant on scheduled handbook inspections. Employees typically depend on their ‘intestine intuition’ – honed with years or many years of sensible expertise and coaching – to make an correct analysis and prescribe the simplest plan of action. And if an unscheduled outage does happen at any time, the prices of misplaced manufacturing can mount shortly whereas finding a suitably certified skilled to attend web site.
This altering operational panorama opens up new prospects for industrial organizations to faucet into the technical assets, innovation and expertise of a world-class associate like ABB, complementing and enhancing their very own capabilities. By way of a consultative method ABB may also help shoulder the burden of caring for and optimizing complicated electrical programs. With the supply of technical experience and assist companies, this consultative method frees up companies to concentrate on KPIs like plant uptime and sustainable development as they embrace the alternatives of power transition and a internet zero future.
ABB, for instance, helps industrial organizations proactively handle their effectivity and sustainability challenges by means of its Electrification Service enterprise. This gives a holistic method to maximizing the well being {of electrical} programs through an overarching view of shoppers’ operational, business and wider strategic targets. Distant monitoring can be utilized to trace the baseline well being and situation of programs, assisted by knowledge analytics to unearth important insights about system efficiency. This intelligence might be harnessed to determine alternatives for power financial savings and extra environment friendly working practices. Simply as importantly it might probably inform condition-based upkeep methods. These prescribe service interventions on the precise efficiency of a tool and its chance of impending failure, slightly than counting on handbook inspections carried out at arbitrary intervals. In addition to lowering the chance of sudden system outages, this condition-based method can provide important price financial savings, with fewer elements which are nonetheless completely serviceable being needlessly thrown out or despatched to recycling