ETH Zurich, in collaboration with ROK Architects, has launched a brand new method to material-saving and round development by way of the Cadenza concrete staircase. Put in within the NEST constructing in Dübendorf, Switzerland, the staircase showcases a novel fabrication technique that minimizes waste and permits for future reuse, embodying the ideas of sustainability and architectural innovation.
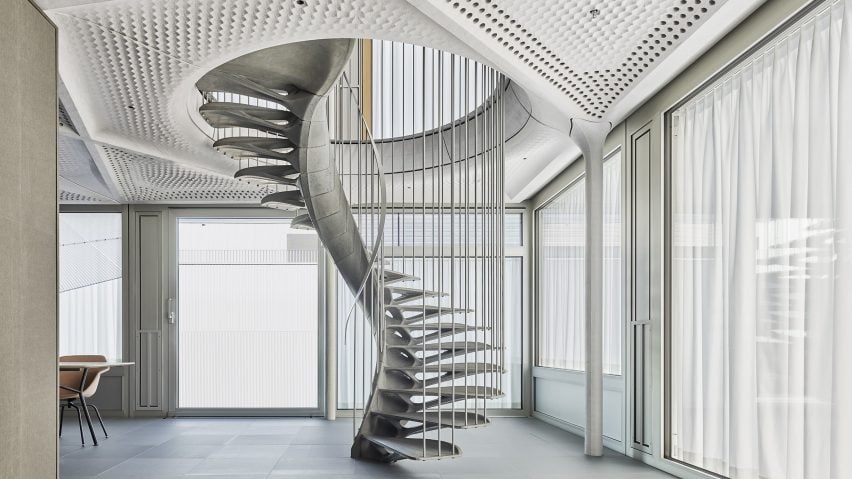
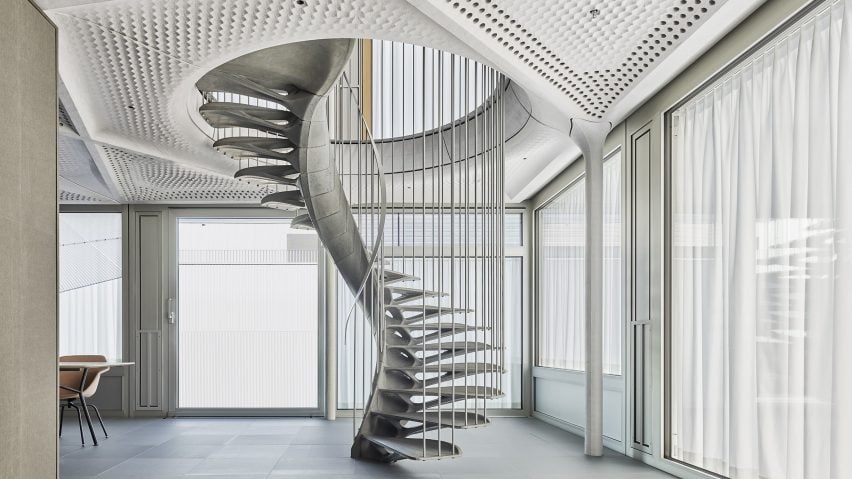
A Reusable, Waste-Lowering Design
The Cadenza staircase, designed as a part of the experimental NEST constructing, options 16 prefabricated concrete steps organized in a smooth spiral. These steps have been all produced utilizing a single 3D-printed mould constructed from carbon fiber-reinforced PET plastic, providing a big discount in waste in comparison with standard single-use concrete formwork. The reusable mould ensures that a number of steps will be created effectively with out the necessity for added fabrication processes.
The steps, that are solely 20 millimeters thick, are made from ultra-high-strength, metal fiber-reinforced concrete. Weighing simply 45 kilograms every, the steps are 60% lighter than conventional concrete steps, because of superior materials optimization strategies.
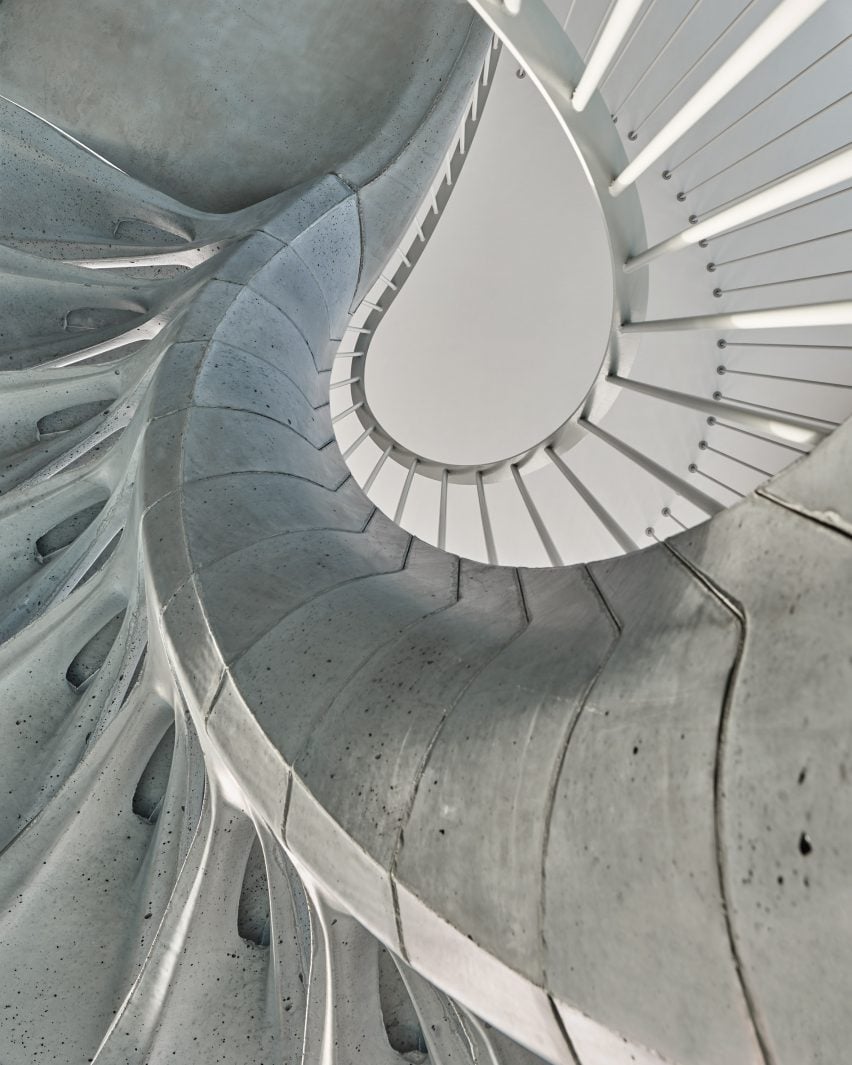
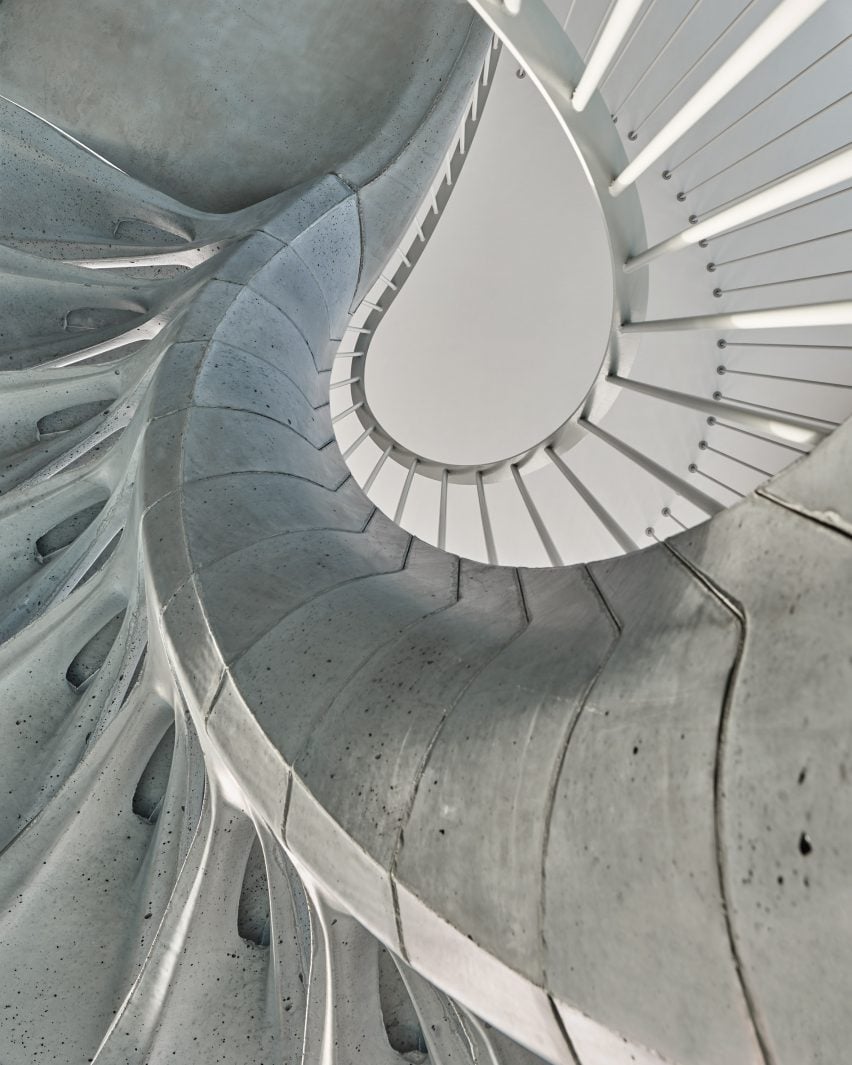
Digital Instruments for Precision and Efficiency
Led by Benjamin Dillenburger, the top of ETH Zurich’s Digital Constructing Applied sciences group, the venture leverages digital design-to-production frameworks to realize excessive precision and materials effectivity. “Digital instruments provide important benefits for custom-made concrete buildings,” says Dillenburger. “This technique reduces waste and enhances structural efficiency, all whereas permitting for architectural expression.”
The computational workflow developed by ETH Zurich and ROK Architects allows the staircase to be assembled off-site and put in in tight areas with out heavy equipment, making it a great resolution for retrofits and different constrained environments.
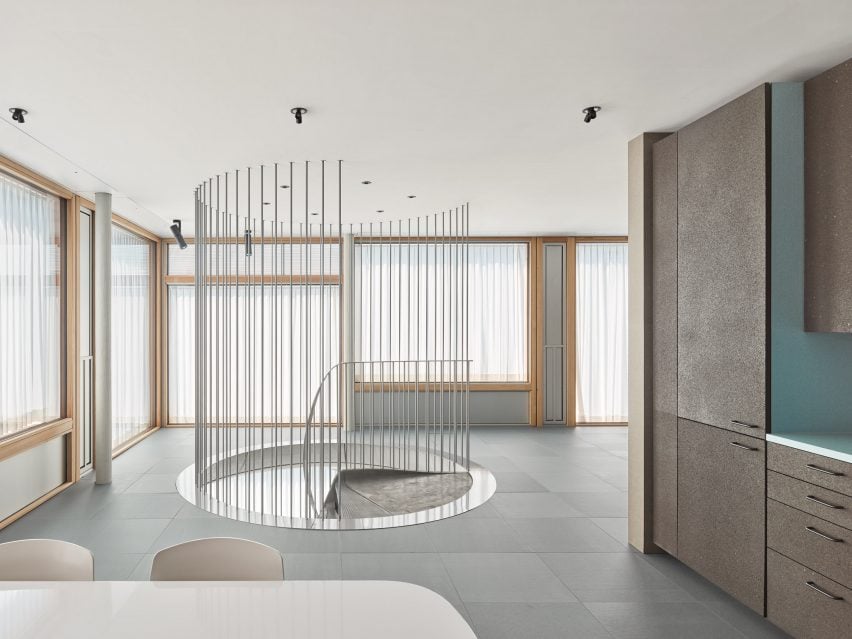
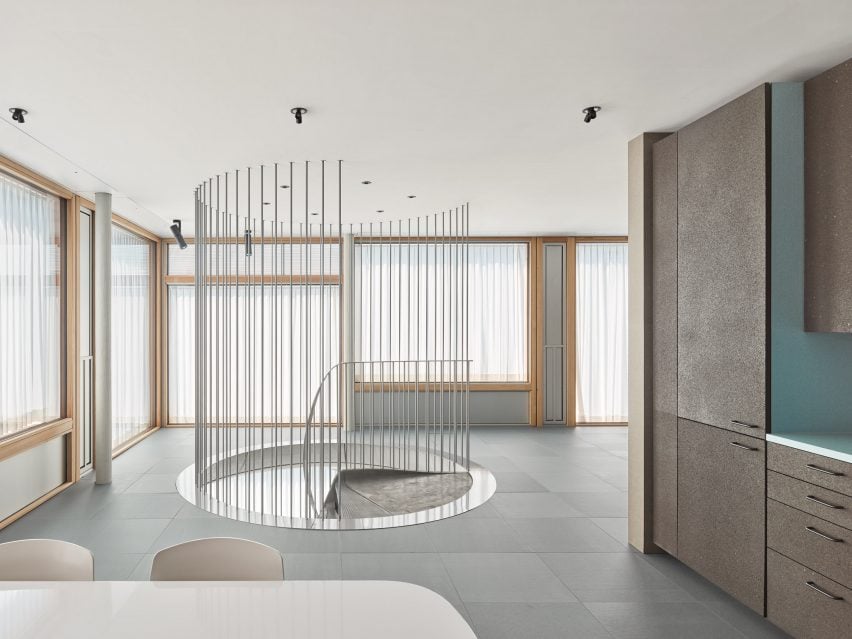
Sustainable and Round Building
The Cadenza staircase is designed with circularity in thoughts. Its steps are held in place utilizing dry connections, permitting them to be simply disassembled and reused in future initiatives. The staircase additionally incorporates a post-tensioning system utilizing reminiscence metal, which is activated by way of warmth to carry the steps tightly collectively. This modern system saves house and simplifies set up, whereas additionally guaranteeing that the construction will be disassembled for reuse.
Incorporating metal reinforcement into the concrete steps, which is usually difficult with 3D printing, additional provides to the staircase’s sturdiness and long-term sustainability. The ultra-high-strength concrete used within the venture is predicted to have a protracted lifespan, contributing to sustainability by offsetting the excessive carbon emissions sometimes related to concrete manufacturing.
Pushing the Boundaries of Building Know-how
The Cadenza staircase is a part of ETH Zurich’s ongoing exploration of cutting-edge development strategies on the NEST constructing. Earlier initiatives have included the HiRes Concrete Slab ceiling with 3D-printed air flow ducts and robotic timber development strategies.
As the development business continues to evolve, ETH Zurich’s Cadenza staircase exemplifies how 3D printing and digital instruments will be harnessed to scale back waste, improve sustainability, and push the boundaries of architectural design.
Supply: dezeen.com