Be part of the Professional Committee for the 2024 3D Printing Business Awards to assist choose the winners!
Equipment manufacturing firm Atlas Copco has considerably decreased manufacturing prices and lead occasions by transitioning to in-house polymer-based AM utilizing EOS know-how.
This shift has decreased manufacturing prices by 30% and lead occasions by 92%, whereas additionally reducing the corporate’s environmental impression by streamlining the availability chain.
Over the previous 18 months, Atlas Copco applied in-house 3D printing for parts utilized in industries akin to automotive. With its consulting division Additive Minds, EOS offered a full resolution past simply the gear, together with cost-per-part evaluation, powder choice, post-processing, and coaching applications. This complete help helped Atlas Copco efficiently transition to polymer-based AM serial manufacturing.
Nathan Rawlings, Gross sales Supervisor at EOS UK, stated, “This undertaking reveals how essential the belief and collaboration is between all events if an organization is to embark on such a dramatic change to its core manufacturing enterprise. No firm ought to really feel that it can’t transition to AM, and EOS helps organizations to verify it’s a success by means of robust communication, cooperation, and a unified group spirit.”
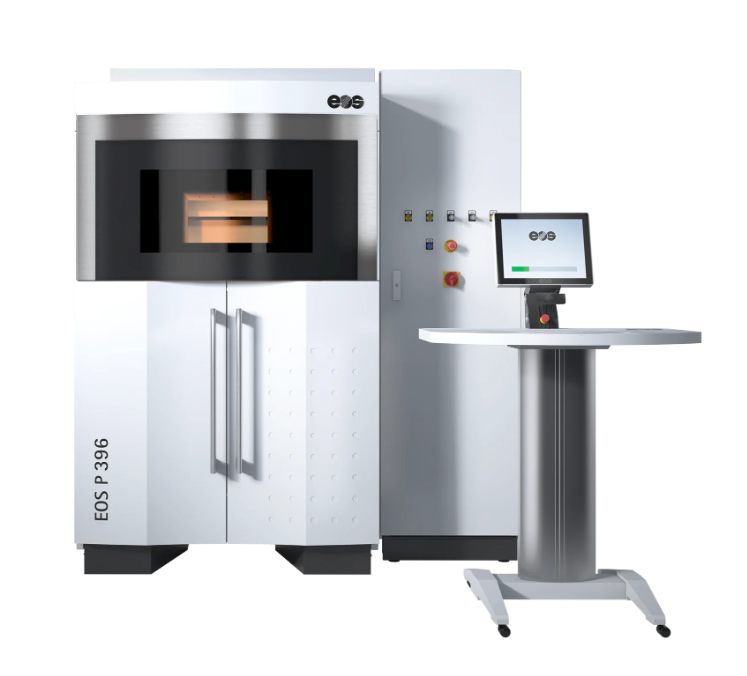
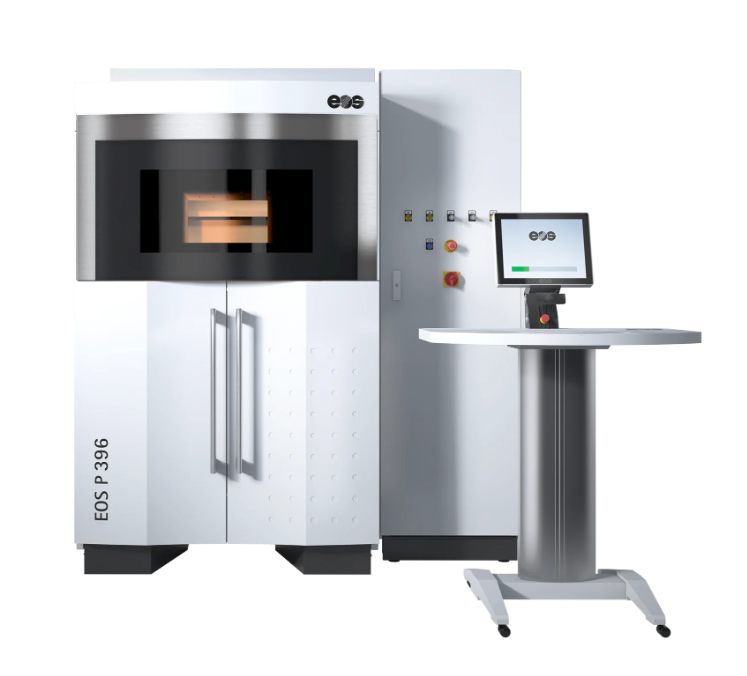
EOS know-how permits large effectivity positive factors
Atlas Copco chosen the EOS P 396 3D printer for its reliability, flexibility, and high-quality manufacturing, supporting 14 supplies and 26 parameter units. Alongside this, Atlas Copco employed the DyeMansion DM60 coloring resolution by means of the EOS accomplice community to paint sure merchandise, together with these utilized in automotive security gear.
By bringing 3D printing in-house, Atlas Copco was capable of cut back its reliance on third-party suppliers, reducing lead occasions from 6-12 weeks to simply 3-4 days. The corporate has additionally achieved near-zero waste, down from round 7%, as a result of precision of the EOS P 396. This shift has additional decreased the environmental impression of manufacturing, as fewer transport sources are wanted.
On account of its funding in AM, Atlas Copco additionally acquired a return on funding (ROI) inside 18 months. The corporate can now prototype new merchandise, simplifying designs and accelerating manufacturing quickly. For instance, a spool service beforehand made by means of casting and machining has been redesigned right into a single, lighter, printed part, which is less expensive to fabricate.
Atlas Copco stated it plans to proceed scaling its 3D printing capabilities, utilizing AM’s flexibility to develop new merchandise whereas remaining aggressive. Its collaboration with EOS and Additive Minds gives ongoing help in course of optimization, enabling Atlas Copco to adapt to future manufacturing wants with larger effectivity.


Is polymer 3D printing a rising area of interest?
Polymer 3D printing has seen elevated use for its customization, price financial savings, sooner manufacturing, and sustainability. Whereas Atlas Copco has leveraged its potential, different entities have explored completely different avenues on this know-how.
Final yr, the POLYLINE undertaking efficiently established an automatic additive manufacturing manufacturing line for large-scale polymer components. Over three years, companions together with BMW, DyeMansion, EOS, and Grenzebach collaborated to advance 3D printing for serial manufacturing at BMW’s Additive Manufacturing Campus. Funded by the German Federal Ministry of Training and Analysis, with €10.7 million, the undertaking achieved automation throughout the manufacturing chain, integrating printing, post-processing, and transport techniques.
In September 2022, researchers on the Metropolis College of Hong Kong (CityU) developed a technique to boost the energy of 3D printed polymeric lattice components by 100 occasions and improve their ductility by partially carbonizing them throughout pyrolysis.
By rigorously controlling the heating course of, the group created hybrid-carbon micro-lattices with enhanced mechanical properties that outperform conventional plastic components. This course of additionally improves biocompatibility, making it appropriate for medical functions akin to coronary stents and bio-implants.
One yr earlier than this, Karlsruhe Institute of Expertise (KIT) researchers developed a technique that mixes Digital Gentle Processing (DLP) with polymerization-induced section separation (PIPS) to 3D print nanoporous polymers with complicated geometries.
This method permits the manufacturing of objects starting from 100 μm to a number of centimeters in dimension, with managed nanoporosity for optimized adsorption, catalysis, and separation. The group printed intricate shapes, together with a hexagonal mesh field, crown, lattice dice, and gyroid, and achieved pore sizes from 10 nm to 1,000 μm.
What 3D printing tendencies do the business leaders anticipate this yr?
What does the Way forward for 3D printing maintain for the subsequent 10 years?
To remain updated with the most recent 3D printing information, don’t overlook to subscribe to the 3D Printing Business e-newsletter or comply with us on Twitter, or like our web page on Fb.
Whilst you’re right here, why not subscribe to our Youtube channel? That includes dialogue, debriefs, video shorts, and webinar replays.
Featured picture reveals the EOS P 396 3D printer. Picture through EOS.