From 3D printed antennas rising 100,000 ft above Earth to futuristic orbital factories and steel elements made in house, 3D printing is reshaping how we construct for house. In three main breakthroughs, NASA, the College of Glasgow, and the European House Company (ESA) show that additive manufacturing (AM) is a gateway to the following period of house exploration. Clearly, AM is not only a instrument however a necessary a part of the way forward for off-world manufacturing.
NASA’s 3D Printed Antenna Soars to New Heights
NASA’s newest experiment has demonstrated that 3D printed antennas may play a key position in future science missions. Engineers from the Close to House Community and Goddard House Flight Heart designed and constructed a 3D printed magneto-electric dipole antenna in simply three months, leveraging Fortify’s superior AM expertise.
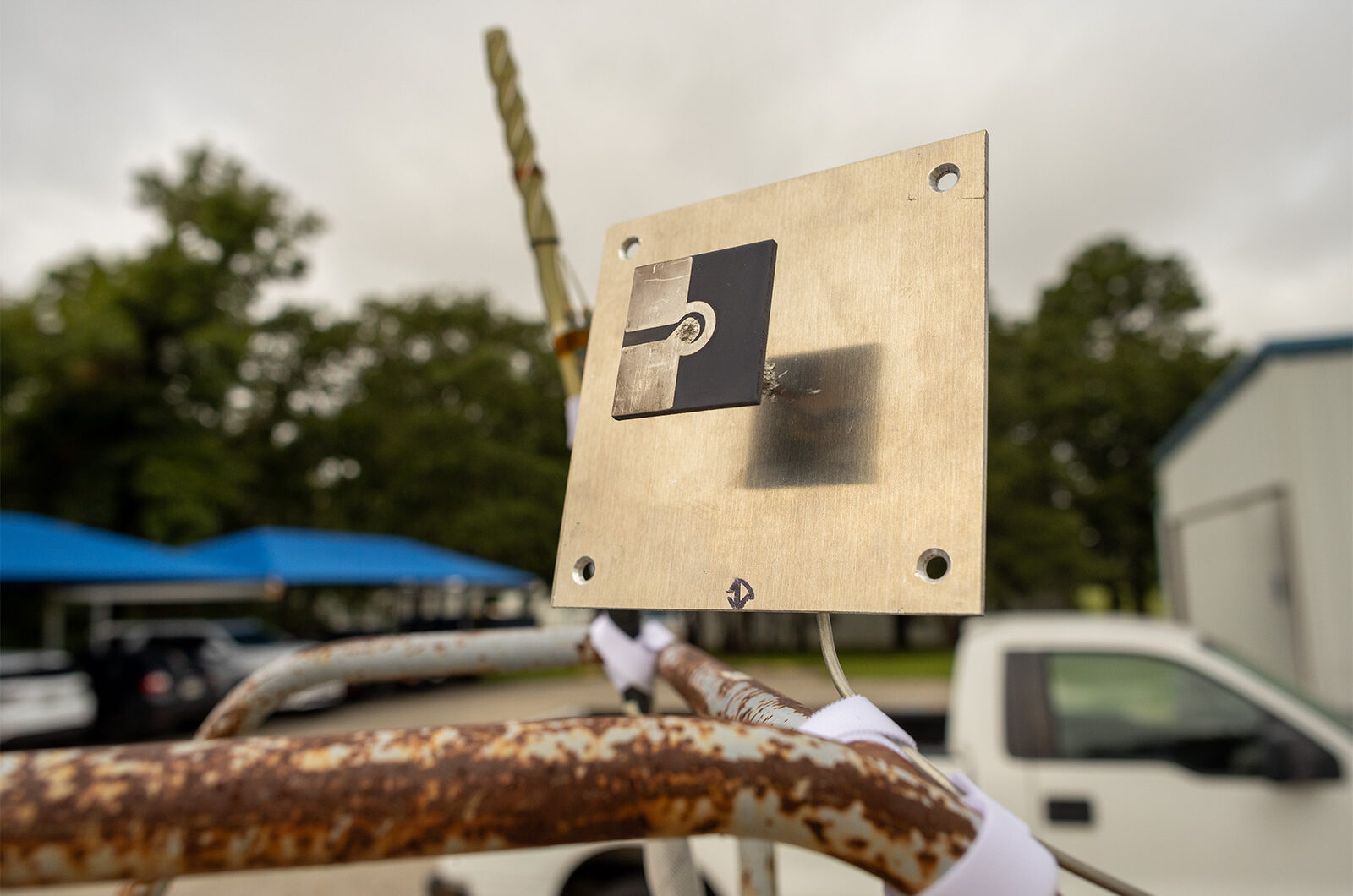
Subject testing was carried out at NASA’s Columbia Scientific Balloon Facility in Palestine, Texas, previous to liftoff. Picture courtesy of NASA/Peter Moschetti.
Engineers from the Close to House Community and Goddard House Flight Heart designed and constructed a 3D printed magneto-electric dipole antenna in simply three months. This antenna was designed for steady and dependable sign transmission utilizing Fortify’s composite 3D printing expertise. Based mostly in Boston, Fortify makes a speciality of printing supplies with fine-tuned microstructures, bettering the antenna’s efficiency.
Not like conventional manufacturing strategies, which might take months to develop and fine-tune, this antenna was printed in hours utilizing a ceramic-filled polymer with low electrical resistance.
As soon as accomplished, the antenna underwent rigorous testing in NASA’s anechoic chamber, one of many quietest locations on Earth, designed to get rid of electromagnetic interference. Engineers then took it to Texas, the place it was mounted on a climate balloon and launched 100,000 ft into the sky.
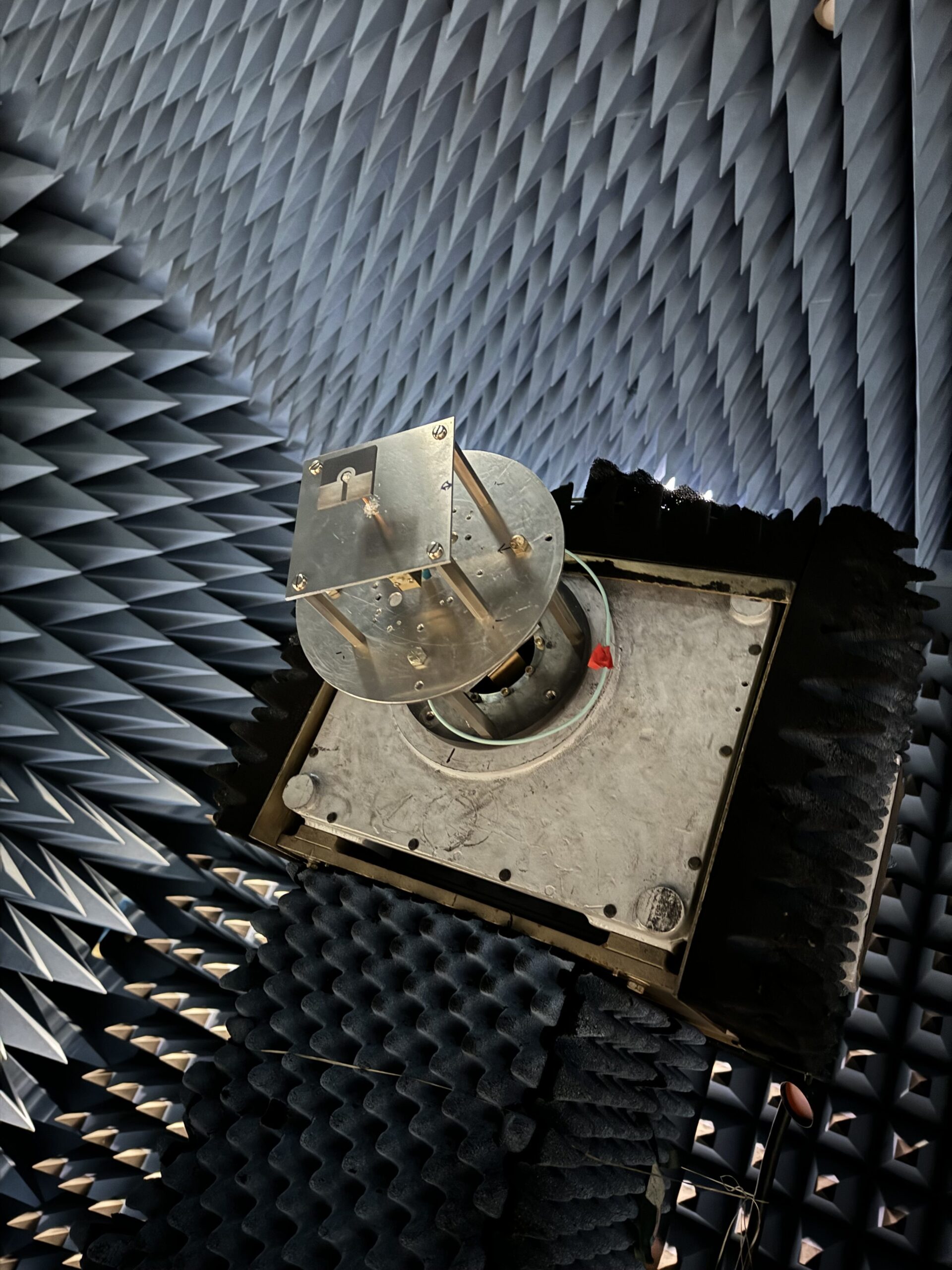
NASA Goddard’s anechoic chamber eliminates echoes and reflections of electromagnetic waves to simulate the relative “quiet” of house. Picture courtesy of NASA/Peter Moschetti
The objective was to check its capacity to ship and obtain alerts in comparison with a standard satellite tv for pc antenna, and the outcomes have been precisely what NASA had hoped for. Not solely did the 3D printed antenna carry out properly beneath excessive situations, however the experiment additionally proved that speedy prototyping may create high-performance communication instruments tailor-made to mission specs. As NASA appears for cheaper and extra versatile methods to help house missions, 3D printing is turning into extra vital than ever.
Printing the Future: A New Period for Orbital Factories
In the meantime, throughout the Atlantic, researchers on the College of Glasgow are tackling considered one of house manufacturing’s largest hurdles: easy methods to 3D print in zero gravity. Led by House Expertise Lecturer Gilles Bailet, a crew on the James Watt College of Engineering has secured a patent for a brand new system designed to perform within the vacuum of house. As an alternative of utilizing conventional filament-based 3D printing, Bailet’s crew developed a granular materials able to being fed to a printer nozzle reliably in low gravity.
To check their prototype, the crew performed experiments aboard a parabolic flight, a analysis airplane that simulates weightlessness by way of sharp ascents and speedy descents. Throughout these 22-second bursts of microgravity, the crew monitored how the printer functioned beneath actual space-like situations, and the outcomes have been promising.
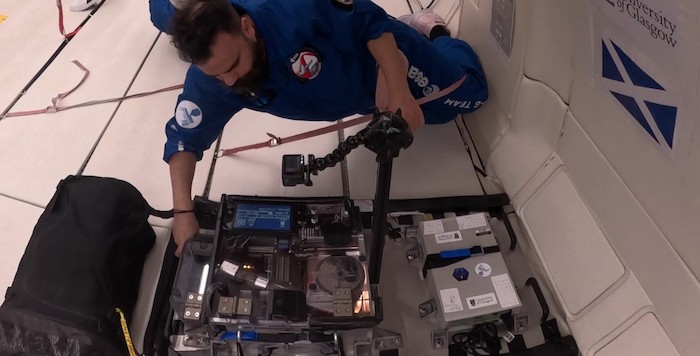
Dr Gilles Bailet along with his prototype 3D printing expertise aboard the “vomit comet.” Picture courtesy of the College of Glasgow.
If profitable in future exams, this expertise may pave the best way for true orbital manufacturing. As an alternative of launching absolutely assembled satellites and tools into house—the place weight and measurement constraints are vital—future missions may deploy modular 3D printers to construct buildings on demand. This might result in the in-orbit manufacturing of photo voltaic reflectors for carbon-free vitality transmission, communications antennas, and even pharmaceutical analysis stations for purer drug manufacturing.
“At the moment, the whole lot that goes into Earth’s orbit is constructed on the floor and despatched into house on rockets. They’ve tightly restricted mass and volumes and might shake themselves to items throughout launch when mechanical constraints are breached, destroying costly cargo within the course of,” Bailet explains. “If, as an alternative, we may place fabricators in house to construct buildings on demand, we’d be free of these payload restrictions. In flip, that would pave the best way to creating way more bold, much less resource-intensive tasks, with methods optimized for his or her mission and never for the constraints of rocket launches.
With their prototype efficiently examined in microgravity, the crew is now looking for funding for an in-space demonstration and dealing with the UK House Company to make sure their expertise aligns with house particles mitigation methods.
Metallic Made in House Lands on Earth
For the primary time in historical past, a steel half 3D printed in house has returned to Earth. The pattern, created in ESA’s Metallic 3D Printer aboard the Worldwide House Station (ISS), landed within the Netherlands at ESA’s technical hub (ESTEC), which can bear rigorous testing.
Developed by Airbus and its companions, the steel printer was put in within the Columbus module in January 2024 by ESA astronaut Andreas Mogensen throughout his Huginn mission. By June, it efficiently printed its first construction—a curved line formed like an “S.” Over the summer season, the printer produced its first full steel pattern, adopted by a second in December.
Now again on Earth, the primary pattern will probably be examined in ESTEC’s Supplies and Electrical Parts Laboratory, the place scientists will examine it to similar samples printed on Earth. The objective is to research how microgravity impacts the steel 3D printing course of and what this implies for future in-space manufacturing. The second pattern will probably be delivered to the Technical College of Denmark for additional evaluation.
Whereas astronauts have beforehand operated plastic 3D printers on the ISS, this marks the primary time steel 3D printing has been achieved in house. The implications are big since future house missions may manufacture important instruments, substitute elements, and structural parts on demand, decreasing reliance on pricey and logistically advanced resupply missions from Earth.
“As missions enterprise farther from Earth, in-space manufacturing will probably be essential for self-sufficiency,” ESA famous in its announcement. “With the ability to 3D print in steel on demand may enable astronauts to restore tools, create new parts, and in the end allow deeper house exploration.”
These three tasks are pushing the boundaries of what’s attainable in house manufacturing. Every breakthrough reveals the nice versatility of 3D printing in environments the place conventional strategies are out of attain.
Subscribe to Our E-mail E-newsletter
Keep up-to-date on all the most recent information from the 3D printing trade and obtain data and gives from third get together distributors.