Dutch firm Additive Industries, which first unveiled its flagship MetalFab industrial 3D printing system in 2015 and formally launched it in 2017, was very busy final 12 months. At Formnext 2023, the metallic 3D printer producer showcased the MetalFab G2, however on the 2024 commerce present, the most recent iteration—the MetalFab 300 Flex—was on show. The Flex, so named for the flexibility to vary its construct platform measurement, generated a whole lot of market consciousness, in response to Strategic Advertising and marketing Director Kartik Rao, who can be a participant in our upcoming Additive Manufacturing Methods summit. He and I not too long ago had a chat in regards to the firm’s printers, purposes, and extra.
“We haven’t been one of many largest metallic AM gamers, however I believe the Flex launch generated some market traction,” Rao advised me. “We bought extra leads at Formnext than earlier than, in order that’s trending in the suitable course for us.”
The launch buyer for the MetalFab 300 Flex was Dutch 3D printing service bureau K3D, which bought two techniques to serve the automotive, industrial, vitality, aerospace, and protection markets. Rao stated that with the unique MetalFab, individuals “unflatteringly referred to it as ‘the bus,’ as a result of it’s a very lengthy system with all of the automation.” However the Flex is a extra accessible machine for individuals simply getting began in metallic AM and with a a lot smaller CapEx.
“It’s initiated discussions with clients that I believe wouldn’t have come to us earlier than,” he stated. “What we’ve been in a position to see is certainly many extra alternatives increase within the pipeline now for that system. It’s been profitable for us, and we have been glad to announce K3D as a buyer.”
A service bureau like K3D was actually “a great use case” for the Flex, in response to Rao, as a result of it wanted the versatile construct measurement “with out having to hold all the fee overheads of a giant system.” However different thrilling alternatives have been arising for the system, and the corporate’s different printers, in new markets as effectively.
RF Antenna Parts
Rao stated the corporate already had a powerful set up base in France and the Netherlands, however that it’s beginning to see extra traction in different elements of Europe, resembling Germany, Italy, Scandinavia, and Switzerland; this final is mirrored in Swissto12. It was introduced at Formnext that the Swiss startup had bought 4 of the corporate’s dual-core MetalFabG2 fashions to make its radio frequency (RF) antenna parts for low Earth orbit (LEO) satellites.
“That’s a booming market,” Rao stated. “I believe it’s a kind of killer purposes for metallic AM.”
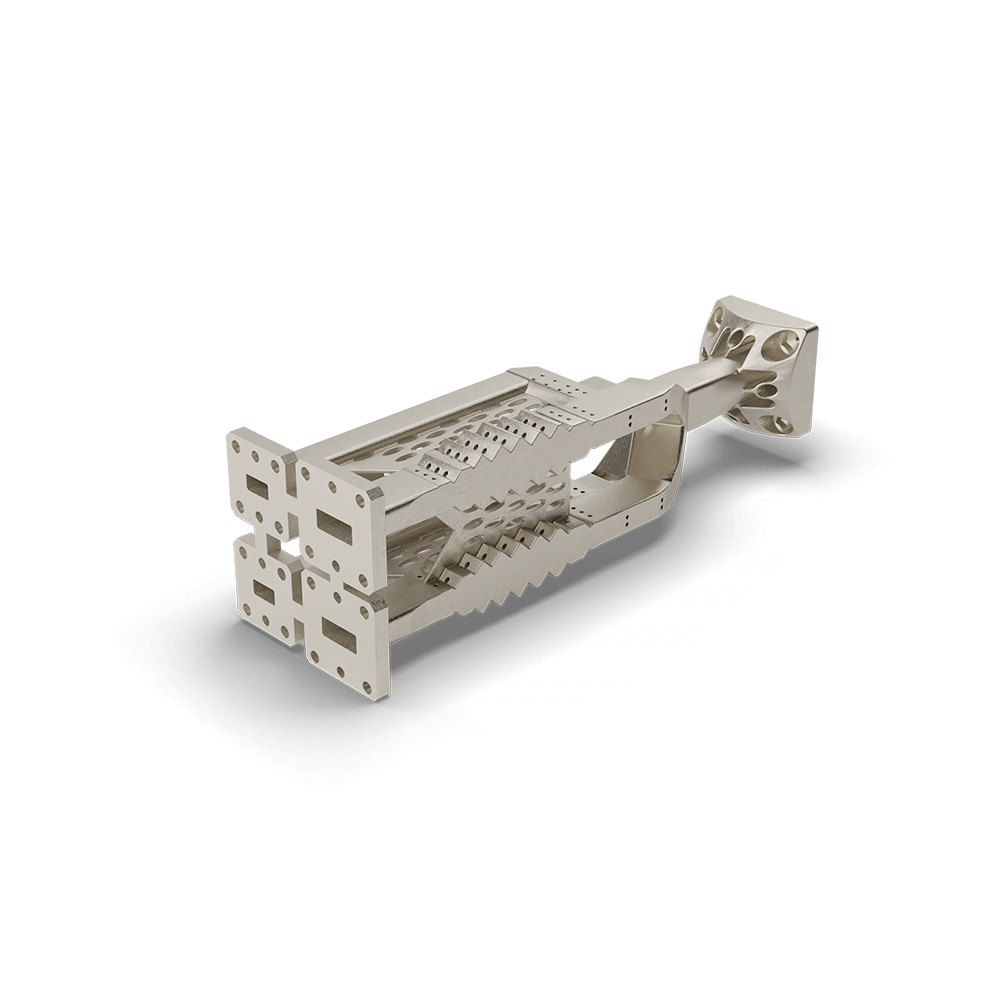
A monolithic Ka-band feedchain, which beforehand would have needed to have a number of elements assembled. Picture courtesy of Swissto12.
Constellations of LEO satellites are wanted for Web connectivity on telephones, so that could be a booming market certainly! Kartik defined that by utilizing metallic 3D printing for waveguides and antenna arrays, you now not want a lot of further joints and screws, as a result of a number of elements might be consolidated into one, which is one other “purposeful profit.” Plus, the know-how permits for extra complicated designs.
“So these are all of the explanation why you’d make that software with metallic AM, however I believe what’s actually fascinating is they might have gone to some other machine vendor to make elements. So why did they arrive to Additive Industries?”
There are probably a number of causes for this, beginning with the corporate’s full area lasers, which signifies that “each single considered one of our lasers can sweep all the way in which throughout the construct plate.” This, together with the printer’s bigger construct measurement, permits a lot better management of dimensional tolerances. Another excuse is the printer’s built-in automation options, resembling construct setup, laser calibration, and built-in powder dealing with. The ultimate motive Kartik talked about for firms that make RF antenna elements to make use of Additive Industries’ know-how is productiveness, as its techniques are modular.
“You’ll be able to add a second core to your system, and what which means is that the optic chamber can transfer backwards and forwards throughout the 2 cores. So while you’re cleansing one out, the opposite one is printing, and when that finishes, it slides throughout and begins printing on the following one. So that you by no means have any laser downtime.
“So maximizing the laser uptime is vital to productiveness. And that’s, once more, the automation kicking in.”
As Rao stated, RF parts appear to be a “candy spot” for Additive Industries, “along with the opposite purposes which have been confirmed on our system, like rocket parts.” Should you’re trying to print the “massive bell” of a rocket engine, you’ll want a much bigger 3D printer than what Additive Industries gives. However the smaller parts above the bell, product of Inconel, is “a incredible candy spot for the MetalFab.”
LPBF for Automotive
I remembered that one of many main purposes I noticed showcased in numerous elements on the firm’s Formnext sales space in 2023 was automotive. There have been a number of System 1 elements, in addition to a small, hole tooling nozzle used to safe the window frames of mid-sized Volkswagen SUVs. Within the automotive, the window is glued to the body, and the nozzle deposits a skinny line of glue across the body so rubber foam might be connected.
“This undertaking, born from the collaboration between Volkswagen and Additive Industries has demonstrated the numerous enterprise case advantages, particularly by way of value and time, that the MetalFab system can deliver within the Automotive mass manufacturing sector,” in response to the introduction to a case research in regards to the nozzle.
Rao referred to as the automotive market “fascinating” and stated it represents about 10-15% of the corporate’s set up base. I requested if he had any ideas about automotive tendencies within the close to future, and he believes that there can be “a renewed concentrate on laser powder mattress fusion inside automotive.”
“Over the previous few years there’s been a whole lot of consideration on binder jetting, however I don’t suppose binder jetting has fairly labored out in the way in which that the automotive firms thought it might,” he stated. “There’s challenges with reaching the suitable prices and the suitable half high quality and so forth. For this reason I believe there’s going to be a renewed concentrate on laser powder mattress fusion over the approaching years, which is sweet for us.”
He additionally believes a few of the bigger firms will develop into extra engaged with automotive, as Additive Industries is “seeing curiosity each within the U.S. and Europe now on the automotive facet.” Rao additionally famous that tooling—one other Additive Industries software—is “actually the driving force for the automotive business” in Europe, whereas he sees “extra emphasis on the precise parts themselves moderately than the tooling elements” within the U.S.
“I believe persons are beginning to notice it’s these industries moderately than industrial aviation, that are actually gonna be pushing ahead,” he stated with reference to automotive 3D printing. “Like 10 years in the past, there was a whole lot of press about industrial aviation adopting metallic AM. However I haven’t actually seen it within the volumes that they have been initially claiming.”
Course of Monitoring
Circling again round to Formnext, Rao stated the corporate additionally marketed a course of monitoring device equipment by means of a collaboration with Additive Assurance. The Australian firm has a chunk of {hardware} referred to as AMiRIS that sits on the entrance of MetalFab techniques for in-process monitoring, which is “changing into more and more helpful in metallic AM as a result of individuals need to have the ability to reduce down on the post-printing prices.”
“Individuals are spending some huge cash post-printing doing X-ray CT scanning, and the CapEx for that’s vital,” he stated. “After which the those who you’ll want to rent and the quantity of experience that goes into all of the studies and the whole lot else is kind of vital. So any financial savings that might be made, and avoiding the quantity of CT scanning that folks do, is useful. And in addition something that we will do to cut back the quantity of validation testing that persons are having to do, like continuously printing tensile bars.”
Everyone seems to be bored with seeing construct plates simply stuffed with tensile check specimens, however how do you get across the want for testing? Rao says that a part of the answer for this “ache level” is course of monitoring, which might help scale back prices. The AMiRIS equipment developed by Additive Assurance will also be used on a number of printers, which he believes could be very helpful.
“We very very similar to working with third events as a result of they’re the most effective. They’re making an attempt to create the know-how and so they’re going 5 ranges deeper than we might on this,” Rao stated. “And we’d a lot moderately work with third events like Additive Assurance, who might be the subject material specialists and develop the most effective in school device toolkits.”
Additive Industries needs to have the ability to combine with these third events and stay an open platform “for these further bits of {hardware} and software program, in order that the shoppers can choose and select as they want.”
“We want to be open, that’s a part of our DNA,” he stated. “We need to be as open as we will as a result of the fact is the complete AM panorama is evolving. There’s a restrict to how a lot management you may train and be closed to all these improvements which are occurring round us.”
However he did word that whereas the corporate needs to be as open as doable, they want to take action in a means that gained’t have them integrating the whole lot of their techniques, “as a result of we additionally perceive that there’s a restrict to how a lot the price of the techniques can go up.”
“These aren’t toys, they’re manufacturing machines. So we don’t need to hold including to the fee an increasing number of by including extra bells and whistles to the system,” he stated.
By its modular techniques, Additive Industries offers its clients a alternative with what they add to their printers. The client is aware of “at what value level the enterprise case goes to stay for his or her software,” so it’s of their arms.
Rao advised me that Additive Industries is aiming for one more product launch at RAPID 2025 in Detroit this April, in order that’s thrilling information. Moreover, in only a few weeks, Rao can be attending our AMS 2025 in New York Metropolis, and moderating a Mass Manufacturing part panel about The Metallic Toolbelt, with audio system from DMG MORI USA, Inc., Desktop Metallic, Mantle, and HP. You’ll be able to register for the summit right here.
Subscribe to Our E mail E-newsletter
Keep up-to-date on all the most recent information from the 3D printing business and obtain data and gives from third social gathering distributors.